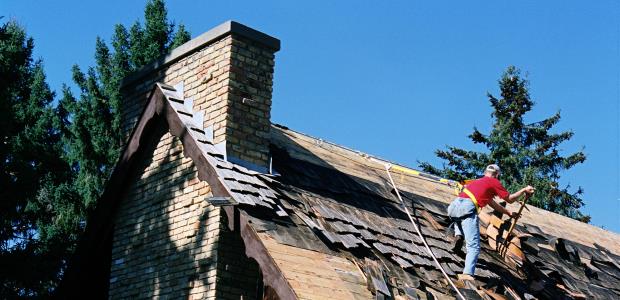
What You Need to Know About Fall Protection Training
Hands-on practice helps to instill confidence and increase competence in users.
- By Marty Breimhurst
- Nov 01, 2014
OSHA requires that organizations provide training to all employees exposed to fall hazards. Yet falls consistently remain one of the leading causes of workplace fatalities, which begs the question, "Are workers receiving the right training?" To ensure your organization is offering the right training program, here are a few key questions to ask.
1. What level of training should my employees have?
There are four levels of fall protection training--awareness, authorized-user, competent person, and qualified-person training. Regardless of the training level, training helps workers recognize the hazards of falling and the steps required to minimize these hazards.
Awareness-level training generally consists of brief, on-site sessions that provide an overview of fall hazards, fall protection equipment, and how it should be used. Many experts do not consider this "training" because it often lacks hands-on practice with equipment and verification of a participant's knowledge.
Authorized-user training is the second level. A best practice to keep employees safe and comply with OSHA is to have any worker exposed to fall hazards undergo authorized-user training. This training is specialized for the type of job and specific fall hazards employees will be exposed to.
The third level is competent-person training. This covers a wider breadth of fall hazards because this employee, typically a supervisor, should understand all types of fall hazards and methods of protection, as well as applicable standards. The competent person needs a higher level of training and knowledge because he or she should be able to address any fall hazard situation in the organization, evaluate it, and recommend solutions. This employee also needs to recognize whether other workers are misusing equipment or working in unsafe conditions, such as on an elevated platform (4 feet for general industry and 6 feet for construction) with no form of fall protection.
The highest level of training is qualified-person training. This person typically has a specialized degree or training that qualifies him or her to address technical situations, such as making certified anchorage points or designing horizontal safety systems. The employer should designate someone who has sufficient training and a reasonable level of knowledge in fall protection in order to be dedicated as the on-site "qualified person."
The same goes for the "competent" and "authorized" levels. The employer must designate who should be trained at what level and ensure the employee gets the training needed to do his or her job safely while helping other workers do the same.
2. How do I select the right trainer?
Once you’ve reviewed your applicable local, state, and federal regulations and determined what level of training your employees need, you must find a reputable organization to deliver it. Referrals from a professional organization or an industry peer can be especially helpful at this stage, as Internet searches on training options can many times lead to countless options.
Once you’ve narrowed it down to two or three options, read the course descriptions and make sure there are clear and decisive training objectives that meet your needs. The trainer should have a measurable standard you can use to evaluate the training, such as "At the end of this course, employees will be able to perform product inspections, set up fall protection equipment, identify anchorage points, and explain OSHA’s fall protection regulations."
Then, ask the vendors about the training experience they can deliver. The ideal training situation is on site or at a training facility that provides ample room for hands-on practice. Generally, a small student-to-instructor ratio is best for this level of training because employees get ample interaction and hands-on time with equipment and techniques. A trainer can show a picture or a video of how to put on a harness, but until employees actually put it on themselves, it's hard to verify they understand and can implement the correct procedures. Putting on a harness, setting up a fall protection system, and climbing using a two-legged lanyard or climbing using a retractable lanyard are invaluable experiences for employees in training. Hands-on practice helps to instill confidence and increase competence in users.
3. What records do I need to keep?
Recordkeeping is important in the event of an on-the-job injury or lawsuit. A court may ask what criteria made an employee a "competent person or authorized user." Employers must cite the training for designated workers and the objectives for the instruction. A court also may look at whether this meets general best practices, as well as OSHA requirements.
Keeping accurate and detailed records will document that an employer vetted the training organization before hiring them. Detailed training records, such as dates and employee attendance, are required in some OSHA mandates, but it’s also in an employer's best interest to document training sessions.
4. How often do workers need training?
Whenever the environment or equipment changes, employees should be retrained. If a worker does not appear to understand how a fall protection system or particular equipment works, that employee also requires further training.
ANSI Z359 recommends retraining every two years, but employers have discretion to shorten or lengthen the time between instruction. After initial training, OSHA considers an employee "trained" unless he or she demonstrates incompetence or the environment or equipment changes.
5. How should I prepare for training courses?
To maximize the benefit of attending training classes, prepare beforehand. If you have questions about specific fall hazards on your job site, take a picture and present this to the trainer. It helps to solve a problem when you can actually see the issue and the environment. Bring your fall protection plan to the training class and review it with a trainer, going through the plan step by step. Ask for advice regarding equipment options, anchorage, or specific roles within the plan.
If applicable, consult with the trainer before the seminar and request permission to bring your own fall protection equipment to the training seminar. The trainer can direct you through the equipment inspection process on your equipment through hands-on exercises.
Think ahead. By being prepared with questions pertaining to your equipment, job skills, or work site, you can tailor the training session to your needs.
This article originally appeared in the November 2014 issue of Occupational Health & Safety.