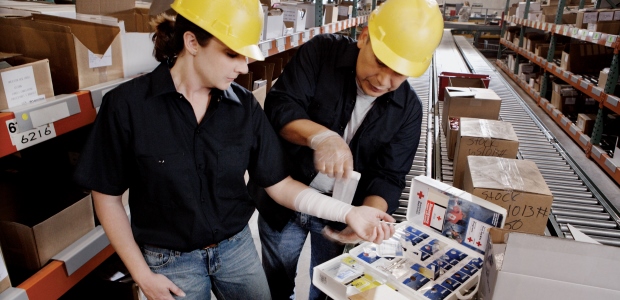
Cut Costs, Not Fingers, with an Injury & Illness Prevention Program
Ensure that employees understand the systems and procedures that are in place, and continue to take their feedback.
- By Jack Rubinger, Brian McFadden
- Sep 01, 2014
How much do workplace injuries cost your company? Costs for accidents vary, so it's hard to give an answer for each injury--but it's easy to find a total. American businesses paid more than $55 billion in 2011 just in direct worker’s compensation, according to the Liberty Mutual Workplace Safety Index. That's more than a billion dollars each week.
That's only part of the cost. In addition to direct payments, facilities lose productivity when a worker can't work, and they lose even more with reduced morale and efficiency. Additional time and resources are spent on repairing equipment, cleaning up messes, and filling out paperwork, including the OSHA 300 form. This doesn’t even count the pain and trouble that the injured worker endures.
"Productivity is essentially the percentage of time a worker is doing what you pay them to do, so illnesses and injuries directly affect your productivity. Saving time is a subset of productivity, and money is an outgrowth of productivity. You don't hire workers to hurt them, and you don't pay them to bleed," said environmental health and safety consultant Phil LaDuke.
Designed as a broad-based plan, OSHA launched the Injury & Illness Prevention Program (I2P2) in April 2010. Although I2P2 plans are the law in many states, including California, Oregon, Washington, and New York, federal OSHA has not yet required that employers establish formal written I2P2 plans.
How to get started implementing an I2P2? You'll need three key elements:
- Participation from management and employees
- Detailed problem identification and control
- Ongoing documentation and improvement
Ken Rogus of McDowell Safety & Health Services said he believes OSHA has gotten no traction on the I2P2 effort, and he prefers using the ANSI/AIHA/ASSE Z10-2012 Safety Management System. "When it comes to the effectiveness of a program, when you see co-workers reminding other co-workers to follow the rules and do the right thing in production, quality, and safety, I think your program, by whatever acronym you want to use, has become effective," he said.
I2P2 has fans in Oregon. "We have an aggressive prevention and root cause incident and injury analysis program. All injuries, no matter how slight, are analyzed with employees, supervisors, and management to get to the root cause with action items to prevent it from happening again. This has vastly helped decrease our OSHA incident rates, workers' compensation direct costs, as well as indirect costs such as lost production time, extra employee training, and allied use of supervision," said Greg Miller, manager of Health, Safety and Security for Gunderson (Lake Oswego, Ore.)
How I2P2 Helps Workers, Customers
Most major companies have some form of an I2P2. Companies with great safety management systems include DuPont, Honeywell, Alcoa, and Kennametal. Those organizations go well beyond meeting the basic core elements that an I2P2 contains. The real success in these organizations is driven by their culture, their value systems, and their ability to make proper decisions at all organizational levels when confronting risks and making risk-based decisions affecting their workers or others.
The strength of an I2P2 is that it defines key elements that should be operationalized to manage risk and safety performance within an organization. The weakness is that they can become paper tigers and collect dust on shelves.
One California consultant is targeting a growing segment of our population with special safety needs: seniors. "For home care companies, employees can be trained to identify safety hazards for themselves and the client. A simple example is finding mold in a bathroom vanity cabinet. The home care client may not know about the problem, but it can represent a health risk to both the client and the caregiver. If the home care agency has an I2P2 and the training, then the caregiver is more likely to recognize the hazard and proactively bring it to the attention of the employer and the client’s family," said Fritzi Gros-Daillon of Household Guardians, which helps California seniors who want to live safely and independently in their own homes. "An effective I2P2 clarifies the roles and responsibilities for safety and communicates to employees that the company operates in compliance with the Cal/OSHA regulations and, in fact, is proactive in hazard assessment and training. It is vital that employees understand that there is a method and opportunity to report safety concerns in the workplace and that there will be follow-up for resolution of the concern."
LaDuke cautioned against trying to make a plan work in a culture that doesn't believe in formal injury and illness prevention programs. "Knock off the lectures or trying to shame them into it. Next, get your facts. Know how much the problem is currently costing, how much your proposed solution will cost, and when will the company see the financial benefits. If you can't answer these questions, you have no business making a proposal," he said.
How to Launch the Program
Before launching an I2P2 program, think about the last facility safety audit conducted at your facility. What items or activities were checked? Were the changes implemented?
Deciding which job(s) should be examined first should be determined by the following criteria:
- Accident frequency and severity
- Potential for severe injuries and illness
- New jobs
- Modified jobs
- Infrequently performed jobs
Inspire your team to get involved. Organize three to five people from your facility representing a variety of departments. Be prepared to walk through and examine equipment and facilities, review the appropriate paperwork and safety signage for all areas, and chat with co-workers who work in many of these areas. Take input from employees in each area of the facility to identify:
- Equipment and tools in use, where they are stored, and how they are maintained
- Work processes and worker movement
- Important elements of the facility itself, such as stairwells, exits, and blind corners
- Anything that could pose a hazard to an employee
- Anything that could be helpful in accident response
Now that you understand the current state of your workplace, look at its history. Examine and record:
- Previous accidents or near misses
- Rates of injury and illness
- Employee turnover rates and absenteeism
- Past costs of workers' compensation and insurance
- Previous hazard reports and improvement suggestions, and what was done in response--or, if nothing was done, why not
Once you understand the existing problems, prioritize and resolve them. Inform workers of what you've found and address any immediate hazard, even with a temporary fix. Then, move forward with more long-term solutions. A final solution may include altering your facility, adding informative signs or labels, or revising a work process. Retrain employees as needed so that all affected workers know what has changed.
"Sometimes simple illness prevention tips--wash your grubby, germ-infested hands--are the most valuable and effective safety communication messages. Also, you need to communicate training and flu shots," LaDuke said. "Signage for emergency eyewash stations, first aid kits, and fire extinguishers is critical."
"The best way to ensure that the I2P2 is implemented and reviewed is the periodic safety meeting schedule. In addition, as jobs change and employees change, the updates should be completed by an administrator. Even quarterly meetings, in-service reviews, or tailgate talks will help keep safety issues present to management and the employees," said Gros-Daillon.
As long as your facility is operating, there will be new situations to deal with and new suggestions to improve on old methods. Instead of fighting that change, embrace it. When periodic retraining is part of your initial plans, it becomes part of the facility culture. Changes don't come as a surprise to anyone. The continuous improvement process becomes natural. Ensure that employees understand the systems and procedures that are in place, and continue to take their feedback.
This article originally appeared in the September 2014 issue of Occupational Health & Safety.