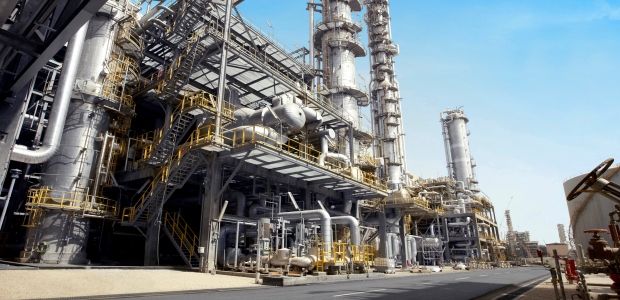
Maintaining Old Technology to Mitigate Safety Risks
We have recently discovered that many petrochemical processing plants should take action on 50 percent or more of their installed gauges.
- By Jason Deane
- Jul 01, 2014
Imagine that you wanted to feel safer in your home. One thing you might do is install a security alarm system. Maybe you even bought the best one on the market with all of the available bells and whistles. But after the alarm was installed, would you stop locking your doors and leave all of the windows open? Of course not, because the alarm system is just one component of your overall safety; it supplements your locks but doesn’t replace them.
Yet I see this exact scenario play out day after day in petrochemical processing plants--inherently dangerous places that have installed fancy figurative alarm systems and then let the doors rust right off the hinges.
Naturally, I’m not really talking about alarms and doors. That is just a metaphor to describe a real problem in the industry: failing instrumentation, specifically mechanical gauges. In fact, it's not alarmist to say that chemical processing plants are on the precipice of a safety crisis, and the problem is much more common than most people think.
The average employee of a petrochemical processing plant is located within 20 feet of 7.6 failing or about-to-fail gauges. When you consider how vital reliable gauge readings are to preventing accidents and warning of mounting danger, that’s a frightening statistic. Even more worrisome is that gauges themselves serve as connection points, so a failing gauge not only ceases to accurately warn of dangerous situations, but also it actually becomes a source of potential media leakage or fire.
How Did We Get Here?
During the past few decades, advances in electronic sensing equipment began to proliferate chemical processing plants of all sorts, including petrochemical refineries. This enabled engineers to monitor most necessary readings from a central control room, and plants flocked to this methodology of process management. For all intents and purposes, this electronic equipment largely replaced mechanical gauges as primary instrumentation.
Understanding the importance of gauges as front-line instruments for floor employees and backup for engineers, most plants left them in place even as they shifted their focus to electronic instrumentation. Proper gauge maintenance, though, fell to the wayside, and years of neglect have rendered many of these instruments unreliable, useless, or even hazardous.
When plants moved toward using electronic sensing instrumentation, they hired specialized electrical engineers to maintain the equipment. Experts at electronics, these engineers lack the skills and experience--or the interest--to maintain mechanical gauges properly. That responsibility used to fall onto the shoulders of instrumentation and control engineers, but their numbers have dwindled due to years of retirements and downsizing. These professionals have typically not been replaced, plants opting instead to hand gauge oversight to technicians in general maintenance departments.
This is where human error takes a toll. Without the necessary education or training to fully understand proper gauge application, maintenance technicians do not have the expertise to consistently identify failing instruments. When they do identify a problem, it is not uncommon for them to replace a failing gauge with an inappropriate SKU not rated to safely handle the application because it looked “close enough.”
How Big is the Problem?
It can be difficult to speak about averages because the number of gauges in need of attention depends on many factors that vary significantly between individual plants. Until recently, the best research indicated that 25 percent of the gauges in an average refinery are failing or about to fail. However, data collected from more than 250 plant audits recently has pointed to numbers that skew higher than previously thought: Many facilities actually are operating with more than 50 percent of their gauges showing unreliable readings.
Every one of these problematic gauges is a risk that could lead to plant shutdowns due to safety lapses or process disruptions. According to OSHA, a single accident costs the average plant more than $150,000. If employee death is involved, that number skyrockets beyond $1 million. That figure doesn’t even include property damage, regulatory fines, litigation, or the bad PR that comes from a high-profile disaster. When you consider that an accident necessitates deployment of more personnel into harm’s way to correct the problem, it’s easy to imagine how quickly these costs can spiral out of control.
Risks aren't limited to the confines of the plant. One of the most concerning issues to EPA is fugitive emissions. These gas leaks originate from weak connection points in piping systems. An average plant contains more than 300,000 connection points, a significant percentage of which are gauges. A failure with any of these connecting gauges can lead to fugitive emissions, which can result in large regulatory fines and even larger penalties if the gas escapes into the environment.
How Do We Fix It?
Properly addressing the issue of failing gauges has two components: Correct the immediate threat first and then implement a plan to prevent future failures. The problem is, most plants lack the internal resources to engage in a project like this on their own, and third-party consultants can be quite expensive. An emerging third option comes from equipment manufacturers that are starting to offer instrumentation audits as value-added services to processing plants that request them.
Regardless of who is ultimately given responsibility to conduct a gauge reliability audit, it's of monumental importance to identify and fix failing gauges as quickly as possible before they cause accidents.
Once affected gauges have been identified and replaced, it's time to begin the work of preventing future problems. The first line of defense for achieving this is education. A little focused training goes a long way. While you can't hope to turn technicians into instrumentation engineers with training, you can teach parameters for recognizing when a gauge needs attention and how to select the proper replacement SKU. Another technique that is quite helpful is performing a storeroom audit and streamlining the SKUs kept in stock. This minimizes confusion when it’s time to select a replacement part.
Even though technology has made many plant processes safer, we should never accept advances at the expense of legacy systems that continue to perform important functions, particularly when safety is involved. Ensuring the integrity of mechanical gauges is an inexpensive process that yields exponential safety and cost-saving dividends.
This article originally appeared in the July 2014 issue of Occupational Health & Safety.