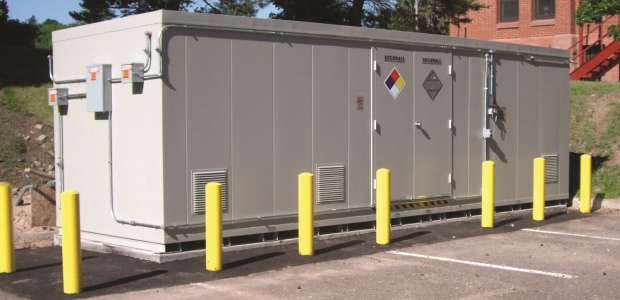
Hidden Hazmat Considerations for Your Safety Program
You will find in the long run that being well prepared costs much less than trying to explain what you did not do after the fact.
Whether working in a small-scale shop or at the mega-corporate local, every safety professional needs to consider potential hazardous materials that employees (or the environment) could be exposed to and related programs that must be updated and maintained. Here are only a few areas to get you started:
- Purchasing. Do you have control, and is safety made aware of what is purchased to ensure it is compliant with your program, equipment, and training already in place? Does safety have purchasing authority for selection or not? It matters in the seriousness of hazardous materials.
- Real estate review. Does safety review sites for prior contamination, stored chemicals left by previous owners or renters as "gifts," groundwater runoff, forgotten USTs, asbestos, lead paint, PCBs, etc.? The list is huge! Do a proper review yourself if you are qualified or hire a consultant to do a site assessment and get the report in writing. Check your neighbors, too, for history, high-hazard inventory potential, and other red flag warnings. Transportation access, river beds, location of nearby railway carriers, coastal flood zones or hurricane-prone areas, fragile populations may cause the rent/sale price to seem cheaper, but the liability can be much greater long term. The greater your hazardous materials use, the more time you should devote to this area and due diligence.
- Chemicals. Review your chemical GHS plan and update what you have on site. Make sure your inventory matches your process, as many managers keep adding new chemicals but never remove data sheets from the inventory and keep leftovers “just in case.” Discuss with your supervisors, department heads, maintenance staff, and everyone who could have input into how to reduce your inventory or change to less-hazardous items when possible while retaining quality. Make sure employees do not bring in unknowns from home, mix items prior to disposal, etc.
- Fire. Do you have appropriate fire protection for the process, materials, and work being done? How do you know? Update as needed and keep a check on replacements, mobile crews, and outside storage areas. Check your storage areas, flammable storage cabinets—no paper lining the shelves!--bonding and grounding issues, LP gas storage areas, and welding and maintenance areas for constantly changing conditions as the work progresses. (Notice any waste oil or antifreeze stored in a milk/veg oil jug anywhere around?) Exit and evacuation drills--do employees understand how to use a fire extinguisher or to evacuate the building and what the alarm sounds like? Do you have a plan in place for hearing/visually/mobility challenged employees? Are your exits clearly marked and kept clear and accessible? How about the basics like electrical safety?
- Waste cleanup. Do you have on hand the needed items to properly clean up and dispose of spills? Absorbents, mats, containments catch basins, shop vacs, bags, mops, etc. Have these on hand and in place and the staff trained how to use it and not drag it through the entire facility on the way out. Think about contamination from an undrained safety shower that put more than 300 gallons of contaminated water on the floor after an employee used it for 15 minutes—what will your second shift supervisor do about it on a Saturday night? Consider your floor materials; will mold/mildew be a problem if there is no hazardous material contamination? (Have you ever seen a hallway of popped floor tiles after a flood? It's a mess.)
- Staff. Are your employees highly skilled, trained professionals? Temps? Students? Volunteers? Undocumented workers with a language barriers? How much liability do you take on every day allowing inappropriately mixed/disposed chemicals, poorly documented procedures, and non-existent training?
- First aid. Does your facility have real first aid coverage for the hazards of the work being done? Make sure it is accessible, available for all shifts and areas of the facility (and mobile crews, too), and that employees are trained how to use it and whom to call for assistance. Are the supplies checked, maintained, and restocked as needed? Do employees know where the closest medical provider is located and how to call for rescue? Make sure your facility address is clearly labeled from the street, too. In an emergency, seconds matter.
- PPE. Do you have a personal protective equipment program or just "some stuff"? Is there a selection process or only a few well-worn catalogs? Know what you need and have on hand what is needed in the correct size and number. Call a professional representative, distributor, or consultant for assistance or do online research. Have medical exams necessary for the use of respiratory protection where needed. Ask questions on what is the best option, such as for gloves as new products for targeted processes are continuously being developed. One of the largest challenges with PPE and protective apparel is staying current in the industry . . . there are so many options to make the employee’s comfort better and to reduce exposure to the contaminant.
- Training. From day one is training being done? Is it understood by the employee and documented? Is it signed? Is it kept on file? Is additional one-to-one training conducted by the immediate supervisor or lead worker for specific hazardous materials, are in-depth skills needed?
The very best safety and hazardous materials program may miss something. We all learn and grow our programs through need, study, and trial and error, unfortunately. Planning ahead helps, and thinking about what could possibly go wrong helps even more to prepare for problems that may cause injury, pain and suffering, environmental damage, and lost production. You will find in the long run that being well prepared costs much less than trying to explain what you did not do after the fact.
This article originally appeared in the July 2014 issue of Occupational Health & Safety.
About the Author
Linda J. Sherrard, MS, CSP, is Safety Consultant II with Central Prison Healthcare Complex, NCDPS in Raleigh, N.C., and is the former technical editor of OH&S.