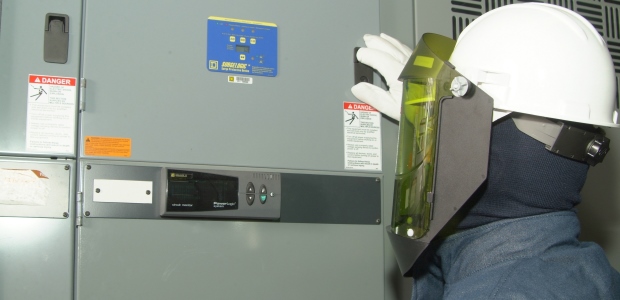
Maintenance of Electrical Distribution Systems is Critical for Reliable Operations and Improved Safety
Little attention or thought is given to these critical assets until a failure occurs. With a little thought and planning for maintenance, most electrical system failures can be eliminated.
- By Joseph Weigel
- Jun 01, 2014
Five to 10 times every day in the United States, a worker will be seriously injured in an electrical workplace accident. The accident statistics indicate that approximately once each day someone will die as a result of an electrical workplace accident. Awareness of these statistics in recent years has resulted in the expansion of existing safety standards that define best practices for workers who work on electrical systems.
The most important of these standards is the NFPA 70E Standard for Electrical Safety in the Workplace®. In recent years, NFPA 70E has evolved to increase awareness and develop best work practices around a hazard called "arc flash and arc blast." In the past, arc flash and blast hazards were not as well understood as was the hazard of electric shock and possible electrocution. The understanding and awareness of arc flash and blast hazards have developed substantially since 1999.
A Fundamental Electrical Safety Principle
Electrical injury accidents are only possible when someone interacts with electrical equipment that is electrically energized, usually by opening the enclosure to expose energized components and circuit parts, racking a circuit breaker out of its cell, or some other unusual physical interaction. Because of this fact, the most fundamental safety principle is to de-energize the equipment before anyone interacts with it in this way to expose himself to potential electrical hazards.
The practice of de-energizing electrical equipment is called lockout/tagout and is often abbreviated as LOTO. It is a very specific set of procedures that must be performed only by trained and qualified persons who are wearing electrical personal protective equipment. Once the equipment has been verified to be in a de-energized state and all of its sources of voltage have been locked out to prevent it from being re-energized during the work, electrical accidents are not possible.
There are some situations that are likely to require or justify work on energized equipment. These justifications are very specifically defined in the standards, and usually the decision to work on energized electrical equipment must be documented by a signed authorizing document called the energized work permit. For the majority of electrical work, including scheduled maintenance, de-energizing is the fundamental requirement for safety.
Electric Power Controls Everything
Electrical distribution and control systems are the heart and circulatory system of any facility. Without a reliable source of electrical power, operation of any facility would not be possible. From manufacturing processes to lighting, security, and environmental controls, nothing will operate without a reliable and continuous flow of electricity.
In spite of the critical nature of electrical equipment, regularly scheduled maintenance has not typically been a primary focus in most facilities; indeed, many facility managers do not think about maintenance until a disruptive failure in the system occurs. Neglecting the maintenance of electrical equipment over a long period of time will inevitably lead to a process-interrupting and damaging system failure. Neglecting maintenance will create elevated safety and property risks, as well.
Out of Sight, Out of Mind
The very nature of the equipment itself probably contributes to this pattern of maintenance neglect over long periods of time. Electrical equipment is very well designed to be safe to operate and to have a long service life, often spanning several decades. By its nature, it is usually hidden out of sight, and awareness of it is seldom raised as long as the lights come on and everything operates as expected. It might also be true that the careful design and quality manufacturing of electrical equipment and its resulting long-term reliability also leads to maintenance neglect. In that respect, one might say that it is the victim of its own high quality and reliability.
The Nature of Electrical Equipment Components
Electrical equipment can be thought of as having two types of components that could be termed "active" and "passive." Passive items are components such as structural support framing, steel cover panels, copper bars to conduct electricity, cables, insulation systems, and the like. These components do not physically move about under normal operating conditions. Once the equipment is properly rated according to the system electrical conditions and installed safely in accordance with applicable codes, these passive components don't require much maintenance, other than periodic cleaning and tightening of attachment hardware.
Active components are current-carrying or current-detecting devices that utilize combinations of electromechanical mechanisms and digital circuits. Their sole purpose and function is to continuously monitor equipment operating conditions to make sure that an abnormal condition can be quickly detected and then to respond rapidly to it to protect the equipment. These devices are usually called by names such as circuit breakers, overcurrent protective devices, protective relays, fused devices, and others. They function as protective devices for the system. They are not primarily designed to protect people, only the equipment and the system.
Under normal operating conditions, both active and passive components operate normally. Circuit breakers, fuses, and protective relays normally operate with their current-carrying contacts (or fuse elements, in the case of fused devices) in a closed position. As soon as a protective device detects an abnormally high current condition (such as a short circuit or arc flash), they are designed to open rapidly to protect the system and minimize the damage.
During an arc flash event, the time to open the circuit is especially critical because the fault clearing time is one of the most important factors that determine how much arc flash thermal energy will be released. If a worker is working on the equipment when this happens, a faster clearing time will reduce the hazardous energy that is released. How quickly this happens depends on many factors, including the characteristics and settings of the devices and the maintenance condition and settings of the overcurrent protective device.
The most important point to remember, though, is that the fault clearing time of the overcurrent protective device just upstream from the fault condition is the most critical aspect of its function, both for protection of the system and, as it happens, protection of anyone who might be working within the flash protection boundary, as well. For instance, it is well known that the thermal energy released in an arc flash event is directly proportional to the fault clearing time. So if the duration of the fault (before the upstream device opens) is doubled, the energy released will also be doubled.
The Consequences of Ignoring Maintenance
But when electrical equipment maintenance is deferred year after year or the equipment maintenance is never performed (and in practice. this is a fairly common condition), it is highly likely that the opening operations of these protective devices will be slowed down. In the worst cases of long-term neglected maintenance, the moving parts in the protective device mechanisms will become seized up because of lubricant failure in pivots and bearing surfaces, so that they cannot operate at all. Circuit breakers that have failed in this way often cannot even be opened mechanically. In that condition, system and property damage from a fault condition is usually very extensive, and arc flash hazard energies will become impossible to calculate. This is a very dangerous situation!
These active components or devices are not like most electromechanical devices that we interact with every day. For example, if your automobile or refrigerator fails for some reason, it becomes apparent to you very quickly that some critical failure has occurred and that repair or maintenance is needed. We all know this very well since we all have had that experience before and it is second nature to us to anticipate maintenance needs.
We know the potential consequences of poor maintenance on our automobile, for example, and we know the potential downside (including the cost) of never changing the engine oil. Electrical circuit protective devices are different in that way. There is no "check engine" light on a circuit breaker, so human knowledge is needed. Good resources exist to provide maintenance requirements for electrical systems.
It Can't Tell You When It Fails
Circuit breakers and similar protective devices normally operate in a "contacts closed" position to carry current to the load. When they fail, they usually fail in that closed position, and they will usually continue to function to carry current to the load. In other words, there is usually no external indication that the protective device has failed. Devices operating in this failed condition can do so indefinitely because there is no indication at all from the device that indicates it has failed or to otherwise signal the need for maintenance.
The failure will become apparent only when an overcurrent condition (or worse, an electrical accident) has occurred and the device opens too slowly or perhaps fails to open at all to mitigate the fault condition. Another way to document the condition of the device is to have diagnostic testing performed on it by a qualified testing company to document its operation. Once testing is done, conditions that are outside of optimal design parameters can be corrected and preventive maintenance can be performed, as well.
Maintenance requirement for electrical systems will vary widely, depending on the type of device, voltage ratings, and the device functions. Typically, passive structural components, such as busbars, cable lugs, insulation system components, and other passive materials, require only cleaning and tightening (unless some physical damage has occurred such as flooding or some other kind of external damage has occurred).
A Few Basic Examples
Many small circuit breakers (typically rated 400 amps and less) called molded case circuit breakers are sealed units and are designed to be reliable over their service life without any need for maintenance. In fact, opening the molded case will usually void any warranty and render the device inoperable. If for some reason one of these units fails, a replacement should be provided. Molded case circuit breakers are usually rated 600 volts or less in electrical systems in the United States.
Larger circuit breakers (commonly called low voltage power circuit breakers) are electro-mechanical devices with either digital trip units or older electro-mechanical trip units. Power circuit breakers definitely require maintenance. These are the most likely to fail if regular maintenance is not performed. These devices are usually classified in voltage ratings of 1,000 volts or less, an industry classification called "low voltage." Low voltage power circuit breakers are usually rated between 800 and 6000 amps.
Medium voltage circuit breakers (usually above 1,000 volts) are very large and highly complex devices. In most industrial and commercial facilities in the United States, these may be found either in the service entrance equipment or fairly high up in the hierarchy of the electrical distribution system. Because of their complexity and large size, their maintenance requirements may be quite extensive. An in-service failure of one of these will usually initiate a very disruptive and long-term outage in the facility.
Low voltage power circuit breakers and medium voltage circuit breakers often can be replaced using various "retrofit" breaker options if an original replacement device is not available. Often because of age, these OEM replacement devices are no longer available from the original manufacturer, so a retrofit often will offer the best choice to avoid replacing the switchgear in its entirety, which can be a very costly and time-consuming project.
Planning for Maintenance
De-energizing the electrical system is the fundamental requirement for safety during maintenance. Because de-energizing by its nature is disruptive to continuous facility operations, it is best to anticipate and plan in advance for maintenance and plan for a facility-wide shutdown over a holiday period or other time when the operational disruption can be minimized, if that is possible. Maintenance shutdowns involve cost and require careful planning, so pre-planning and budgeting are essential to anticipate the need for it. If the facility does not have qualified staff personnel to perform the maintenance, there are many qualified service companies that offer these services.
Considerable knowledge has been gained over the years about how to properly maintain electrical systems. This knowledge has been documented in a consensus standard titled NPFA 70B Recommended Practice for Electrical Equipment Maintenance® 2013 Edition. Standards like NFPA 70B are developed by volunteer committee members who have extensive knowledge of electrical systems, electrical equipment, installation practices, code requirements, and maintenance and device testing protocols. NFPA 70B is the definitive standard for maintenance of electrical systems, just as NFPA 70E is the recognized reference standard for electrical workplace safety.
Consensus standards like NFPA 70E and NFPA 70B are recommended best practices. They are considered to be recommendations and therefore have no legal enforceability. However, because OSHA recognizes consensus standards such as NFPA70E and NFPA 70B, it often will cite to these standards if electrical workplace accidents happen or if workplace safety violations are cited. Because maintenance of electrical equipment has such a strong causative correlation to electrical workplace safety, these standards often reference each other.
Changing the Maintenance Paradigm
Attention to maintenance of electrical systems is very critical for reliability and for safety reasons, as well. Most organizations understand the costs associated with unplanned operational interruptions, but few executives really think much about the devastating financial and personal consequences of a serious electrical injury or fatality. The electrical systems that support all types of operations are the backbone of every facility, yet little attention or thought is given to these critical assets until a failure of the system occurs.
With a little thought and planning for maintenance, most electrical system failures can be eliminated. Maintenance will not prevent electrical accidents, but it will reduce the hazard levels in the system and potential injuries to workers if an accident does occur.
The NPFA 70B Recommended Practice for Electrical Equipment Maintenance® 2013 Edition will be an invaluable resource for guidance on how to implement a maintenance strategy that will pay dividends on improved reliability and workplace safety.
This article originally appeared in the June 2014 issue of Occupational Health & Safety.