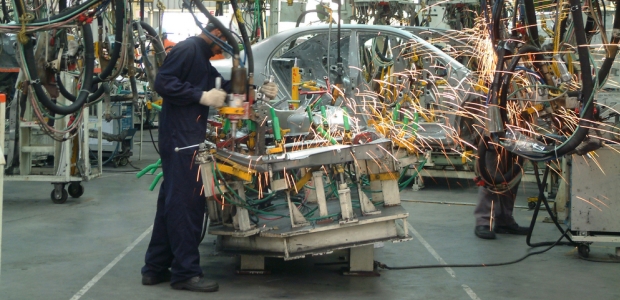
Applying Ergonomics to Industrial Glove Design
Poorly designed gloves force workers to compensate for lack of support, thereby placing unnecessary stress on their muscles and joints.
- By Scott Corriveau
- Jan 01, 2014
Just like helmets and safety glasses, gloves are a key component of a worker's safety gear in the industrial sector. However, the critical protection offered by gloves becomes meaningless when workers refuse to wear them because they are uncomfortable or too cumbersome. Every year, approximately 1 million workers in the United States are treated in emergency rooms for acute hand injuries incurred on the job. According to the Bureau of Labor Statistics, 70 percent of workers who experienced hand injuries were not wearing gloves, and the remaining 30 percent experienced injuries due to wearing damaged gloves or the improper type of glove for the application.1
This is potentially due in part to workers seeking comfort over protection. Adding to the burden of hand injuries, poorly designed gloves force workers to compensate for lack of support, thereby placing unnecessary stress on their muscles and joints.
The integration of ergonomic principles into industrial glove design is not only based on satisfying a need for comfort, it is also critical to worker productivity, health, and well-being. As the industrial market continues to grow around the globe and the workforce steadily increases and diversifies, PPE manufacturers are exploring new ways to customize equipment to better fit the contours of individual workers' hands while also addressing the needs of specific applications, conditions, and duration of work that the gloves will be expected to endure. Identifying these factors and incorporating them into the glove design is the key to creating effective, ergonomically designed equipment.
Although both protection and comfort should be necessary in proper glove design, achieving them requires conflicting designs and constructions. In an effort to prevent cuts and abrasions, which are typically more consequential than hand fatigue, safety managers often rely on gloves that are thicker and bulkier to increase protection. However, these gloves make it harder for workers to function, forcing workers either to repetitively perform the same task despite the fatigue and muscle strain it causes or remove the gloves completely. In an effort to meet production quotas, many pick the latter.
Equipment manufacturers are challenged to find the right combination of comfort and performance while creating products that adhere to the safety regulations that employers must follow. The key to marrying the opposing principles of ergonomics and protection lies in shifting the development process to incorporate the worker's experience at the onset of design ideation and leveraging our insight to develop new equipment technologies. If we learn to understand what workers need--whether it be enhanced dexterity, fingertip sensitivity, moisture management, or liquid repellence--then we can tailor the design of a glove to address these concerns and build the protective features to complement these needs. This might seem absurd in an industry based on providing protective equipment, but advancements in technology have paved the way for new materials that address the comfort and feel of a glove without losing the durability needed to function in industrial environments.
Safety is of paramount importance in any industrial setting, both for worker well-being and overall productivity. Worker demand for comfortable protective equipment is increasing, however. Gloves play an important role in ensuring safety by protecting hands from cuts, burns, and other serious injuries, but unless they offer comfort, performance, and precision, workers may neglect to wear them. As attention to ergonomics continues to grow by the general workforce, hand protection products that are designed to tailor-fit a diverse and global workforce will likely be a requirement for many environments in the future. By collaborating with industry partners and applying ergonomic design principles early, it is possible that worker safety, compliance, and overall productivity can improve.
The Future of PPE
Enforcing safety in the industrial and manufacturing sector must be a collaborative effort upheld by governmental bodies and non-governmental organizations, industry safety officers, and PPE manufacturers. While organizations such as OSHA develop mandates and industry standards to ensure safety, corporate officials modify policies to adhere to new rules and rely on PPE manufacturers to develop equipment that fulfills the standards and allows workers to perform under safe conditions. This collaboration has become crucial in recent years as the global market is experiencing a collective push from multiple countries to modernize, thus driving increases in construction and goods production and generating more jobs.
The PPE market has benefitted substantially from this push due to an increased demand for safety equipment. In fact, Global Industry Analysts, Inc. estimates the global PPE market will grow to $33.3 billion by 2015.2 With the PPE market’s ongoing expansion and the occupational safety community looking toward the future of safety, it is imperative that leaders in equipment development recognize the need to incorporate another key aspect to the safety dialogue: the worker experience.
OSHA constantly implements and enforces new mandates to adjust to modern work experiences, adopting new standards for heat and fire-resistant clothing and hearing protection. However, as several industries continue to expand--the goods manufacturing sector alone is projected to add almost 1.8 million jobs during 2010-20203--undoubtedly it will become difficult to ensure these standards are upheld. Safety officials rely on PPE manufacturers to provide an additional layer of protection for their workers, making the technology that they develop a crucial part to the safety environment yet unobtrusive enough for the worker to still get the job done.
Technology has always been a staple of the PPE market. 3D-modeling and simulation, along with extensive testing through the recreation of conditions and machinery that enables the development of multiple prototypes, allows PPE manufacturers to expedite the creation of new equipment that adheres to standards set by safety organizations such as the International Safety Equipment Association. While it is important that PPE manufacturers continue to utilize technology to meet these standards, it is important for the future of the industry that they also pay attention to what matters to the end user. In a rapidly growing industry, the workers' main concern is not only safety, but also to perform effectively. If their PPE hinders their ability to do so, they will often choose to avoid using it, consequently putting them in danger.
Equipment manufacturers must combine new technology with the needs of the worker to create solutions that matter not only for safety, but also for performance and comfort. The "worker experience" must be included in the formula for new equipment development and essentially drive the products that we create. We can no longer rely only on regulatory standards as a guideline to what our products provide; we must also meet the standards of the workers who will be using our products. In doing so, we achieve a triple win: meeting new and emerging safety standards, protection and safety in the workplace, and productivity to meet the demands of a growing industrial society.
References
1. Shaffer, L. "Where are Your Gloves?" Industrial Safety & Hygiene News. November 2008. http://www.ishn.com/articles/where-are-your-gloves, accessed Sept. 27, 2012.
2. Global Industry Analysts, Personal Protective Equipment: A Global Strategic Business Report Press Release, Oct. 6, 2010, http://www.prweb.com/releases/protective_equipment_PPE/protective_clothing/prweb4603364.htm
3. Monthly Labor Review, January 2012, Industry employment and output projections to 2020.
This article originally appeared in the January 2014 issue of Occupational Health & Safety.