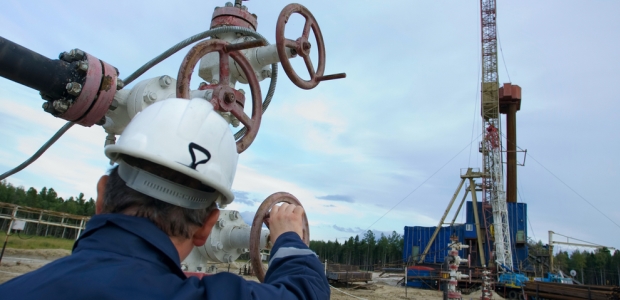
Next-Generation Gas Detection
Commitment to safe practices is required to optimize the protection that advanced technology affords workers.
Gas detection technology has come a long way since the use of canaries to monitor for toxic levels of harmful gases in mines. Today, a wide range of intuitive gas detection technologies are available that safeguard and shield workers from life-threatening events resulting from the presence of carbon monoxide, methane, or other toxic gases. However, to unlock these technologies' fullest potential, the industry needs to commit to the implementation of baseline safety practices to maximize gas detection systems' effectiveness and protect workers while on the job.
Back to Basics
Before taking a deeper dive into how these next-generation gas detection technologies can contribute to a more secure work environment when used by companies with a steadfast commitment to safety, it's important to get back to the basics on how to determine the most appropriate gas detection system for a work site. No matter whether you're purchasing your first, second, or third gas detection system, consider the following questions to identify the system that will best support your site's safety goals:
- What potential worksite hazards exist?
- What alarm response time is most appropriate given the hazards present?
- Does the project require portable or stationary monitoring?
- If portable monitoring is required, what is the most easily worn option that will encourage appropriate use by the team?
- What environmental conditions must the system withstand?
- What type of sensors will be most effective based on the work site hazards?
- How do our employees work best, and will the system integrate seamlessly into existing operations to allow for ease of use?
- What type and how much training is required to maximize the safety potential afforded by the system?
- Would we find value in being able to monitor only a single work site or multiple locations throughout an enterprise?
- How important is it for the system to provide analytics that produce insight into how operations can be made more efficient, as well as safer?
By considering these questions, companies can confidently pinpoint the gas detection system that aligns with both the on-site team’s and the company's needs. Companies will achieve greater efficiency while minimizing the potential for personnel risk breakdowns or stoppages due to toxic levels of gas that can be severely detrimental to personnel.
Safety First
Compromised safety is never acceptable. While the use of gas detection technology contributes to the prevention of life-threatening situations, it is only the first step of many in ensuring complete worker safety. To fully maximize the protection afforded by gas detection systems, companies must ensure their responsible and appropriate use by an educated and trained team and mandate the non-negotiable implementation of the following practices:
- Bump testing: To have total confidence that a gas detection system will alarm workers to life-threatening gas conditions, it is necessary to bump test these solutions with a known concentration of the target gas. Bump testing, which should be completed prior to each day's use or work shift, enables companies and their workers to work confidently because it eliminates any concern about the performance of the hardware and software.
- Calibration: This is a vital step in guaranteeing the accuracy of gas detectors' readings because it confirms that the results will meet or exceed defined criteria. Calibration also assists with determining the condition of the gas detector's sensor, which is extremely important because sensors possess a limited lifespan. For example, oxygen sensors' projected life span is 1.5 to 2 years; catalytic bead combustible sensors' is 3 to 5 years; electrochemical toxic gas sensors' is 1 to 4 years; infrared gas sensors' is 5 to 10 years; and photoionization gas sensors' is 2 to 4 years.
- Regular data review: Gas monitors are fully equipped to tell users when, where, and in what conditions they were used. Regular review is incredibly helpful when aiming to make adjustments to current processes and procedures that contribute to worker safety and greater productivity.
- Alarm settings: For the team's safety, it is imperative that all OSHA and/or ACGIH guidelines and exposure recommendations are followed all day, every day. They are the baseline thresholds for keeping the team out of harm's way. Beyond OSHA, it is also imperative that companies comply with any existing corporate, local, state, and federal regulations.
In addition to the day-to-day testing, there are additional steps companies can take to enhance their workers' safety, including partnering with third-party occupational health and safety associations and organizations. For example, the Voluntary Protection Programs Participants' Association, Inc. (VPPPA) is dedicated to cooperative occupational safety, health, and environmental management systems. Through partnering with organizations such as this, companies can have access to numerous educational materials to grow their workers' knowledge of safety best practices and, in turn, contribute to a stronger company safety culture. Companies also should consider providing ongoing training and education to both short- and long-term employees because a gas detection system is only as effective as those who use it. More education often means less likelihood of a life-threatening event, safeguarding productivity, as well as the company's profit margins.
Training should occur in the following areas to maximize the potential of gas detection systems:
- Hazardous gases present on site
- Limitations of gas detection equipment and sensor technology
- Calibration and maintenance
- Hands-on operation and instrument review
Reinforcing the importance of ongoing training and education is a recent survey completed by Dräger with the American Society of Safety Engineers. "The 1ppm Hydrogen Sulfide Threshold: Are you prepared?" polled ASSE members to determine their awareness of the new ACGIH hydrogen sulfide TLV recommending lower thresholds for detection of hazardous gases and also the preparedness of their organizations to meet this threshold. The study revealed that 53 percent of safety experts in the oil and gas industry are unaware of the new threshold, which looks to prevent incidents related to H2S exposure.
Taking these extra measures could mean the difference between life and death.
Gas Detection Technology 2.0
To further ensure a safer and brighter future for the industry and its workers, equipment manufacturers continue to develop the next frontier of gas detection technology. Combined with an educated and properly trained workforce, this technology creates a safer work environment. Driving this next evolution of gas detection technology are both “big data” and the ongoing integration of wireless technologies, such as apps.
Today, leading gas detection manufacturers have implemented a system for automatic calibration of various products simply by scanning a bar code on the box in which the testing equipment arrived. While this is just one example, companies are exploring the possible application of QR codes on instruction manuals and other documents, codes that ultimately relay users back to interactive tutorials, case studies, and service representatives to contribute to the equipment's proper and safe use.
On a larger scale, the oil and gas industry knows no constants when it comes to climate. From the sub-zero sands of northern Alberta to the scorching plains of west Texas, the industry and its products need to operate in extreme climates. Connectivity to weather patterns, seismic activity, and other natural occurrences are just a few of the monitoring capabilities that are being developed for mobile applications.
A climate app is valuable when everything is running as it is supposed to, but it may be even more important when everything stops running perfectly. In the event of a gas incident, the application's monitors could detect hazardous gas levels at the perimeter of an area and then model spread and exposure risk from additional data, including wind direction and humidity levels. The path of the gas or vapor could be predicted based on wind patterns, allowing for immediate amendments to the evacuation protocol. Ultimately, the device would provide emergency services and personnel with the ability to mobilize swiftly and effectively.
From gas detection to well locators, the oil and gas industry is quickly expanding its app repertoire. Manufacturers of a variety of oil- and gas-related products are bringing their on-site tools and online platforms together, offering drillers and executives a way to obtain real-time, objective information from any location.
Data That Drives Safety and Profitability
Also revolutionizing gas detection technology is the use of "big data." The utilization of information generated by gas detection systems arms companies with invaluable intelligence that provides unmatched insight into their daily operations. In addition to offering insights into how to contribute to a safer and more productive work environment, data also affords companies these benefits:
- Provides insurance companies with more assurances of calibrated equipment throughout the year, helping to reduce the cost of liability insurance
- Eliminates the cost of human error in the maintenance of gas detection systems because data can alert users when the operability of the system's hardware and software is compromised
- Enables monitoring of the entire fleet across the country to analyze daily operations and pinpoint opportunities to increase efficiency and productivity
- Identifies gaps in safety programs that need to be corrected to enhance safety
- Enhances management of the instrumentation fleet through the use of predictive maintenance, contributing to greater internal efficiencies and minimizing the cost of equipment repairs
Beyond being used by individual companies to create efficiencies and greater on-site safety, the data also has the potential to be culled and reviewed by industry organizations, such as OSHA, in an effort to establish more consistent and effective safety guidelines that can keep workers out of harm’s way.
The Next Frontier
So what does the future hold for gas detection technology? Similar to many other industries, from health care to telecommunications, as gas detection systems become increasingly smarter and more intuitive, they will also become smaller and increasingly scalable. Beyond offering greater flexibility, detection systems in the near future also will feature more sensitive sensors that will be able to detect harmful gases at lower levels, offering line workers even more protection.
As these solutions continue to progress and lay the foundation for a safer and more productive tomorrow, it is up to the industry to set best practices and establish more consistent regulations and guidelines surrounding their use to ensure companies can reap the rewards these advanced technologies provide: greater productivity, profitability, and, most importantly, on-site safety.
This article originally appeared in the December 2013 issue of Occupational Health & Safety.