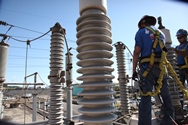
Applying Personal Protective Grounds
Always test circuits for the absence of voltage before placing personal protective grounds. Just because you know it's de-energized doesn't mean that it really is.
- By James R. White
- Jun 01, 2013
Personal protective grounds go by several names in the industry: "temporary protective grounds," "ground sets," "ground clusters," or just plain "grounds." Personal protective grounds are used whenever workers perform tasks on electrical power systems that may become reenergized for some reason, possibly by the reclosing of switches or circuit breakers, static voltages, induced voltages in outdoor substations or lines, and capacitive discharges. While most technicians think of using personal protective grounds when working on higher-voltage systems, they are also needed when working on low-voltage systems, especially when there may be capacitors connected into the circuit (UPS systems and variable frequency drives) or when the circuit may be subject to one of the issues mentioned earlier. The use of personal protective grounding is covered by OSHA 1910.269(n), "Grounding for the Protection of Employees," and the NFPA 70E Section 120.3, "Temporary Protective Grounding." Both sources contain very similar requirements.
NFPA 70E Section 120.3(A) Placement states, "Temporary protective grounds (personal protective grounds) are to be placed so that they do not expose employees to hazardous differences in potential. Grounds cannot be placed too close to the worksite and must be placed or secured so they cannot come into contact with people." Grounds must be placed close enough to protect workers, but not so close that they can strike them if the grounds should become reenergized, especially due to fault-level currents. The current flowing through a ground cable can create a magnetic field strong enough to make the cable snap like a whip, possibly breaking bones or knocking workers off structures.
Linemen must be careful about where personal protective grounds are placed because they must create an equipotential zone and work within that zone. A.B. Chance is one source of information on personal protective grounds and has several good booklets and videos that go into great detail about placing grounds effectively. Figure 1 is a properly designed, properly installed ground set on a pad-mounted distribution transformer. Contrast this to Figure 2, which is very close to an act of suicide.
NFPA 70E Section 120.3(B) Capacity states, "Temporary protective grounding equipment shall be capable of conducting the maximum fault current that could flow at the point of grounding for the time necessary to clear the fault." If the ampacity of any part of the ground set is inadequate (cable, ferrule, or clamp) or if the connection has high impedance due to a poor connection or defect, the personal protective ground cluster could "fuse." That's a fancy way of saying it will melt. Actually, it would probably vaporize, causing an arc flash. ASTM F-855, "Standard Specifications for Temporary Protective Grounds to Be Used on De-energized Electric Power Lines and Equipment," Table 1, provides the required cable sizes to meet the requirements of this paragraph. Table 2 is used when applications have a high X/R ratio. There are two ratings given in Table 1, "withstand" and "ultimate."
From ASTM F-855:
- "3.1.5 ultimate capacity -- this represents a current which it is calculated the component is capable of conducting for the specified time. It is expected that component damage may result. The component shall not be reused, except in test situations.
- 3.1.6 withstand rating -- this represents a near symmetrical current which shall be conducted without any component being damaged sufficiently to prevent being operable and reusable. The protective ground shall be capable of passing a second test at this current after being cooled to ambient temperature."
Table 1 from ASTM F-855
Standard Specifications for Temporary Protective Grounds to Be Used on De-energized Electric Power Lines and Equipment
NFPA 70E Section 120.3(C) Equipment Approval states, "Personal protective grounding equipment must meet the requirements of ASTM F-855, Standard Specification for Temporary Protective Grounds to be Used on De-energized Electric Power Lines and Equipment." This is to prevent people/companies from using chains, welding cables and clamps, automotive jumper cables and other inappropriate types of grounding jumpers. Figure 2 shows a ground that was placed on a transformer by a local utility worker. The steel links, along with their high interlink impedance, make this grounding method extremely dangerous. And no, this is not an old picture! This type of grounding practice is doubly dangerous: 1) it offers virtually no protection at all and 2) whoever placed that ground obviously thought they were protected. Stupid is as stupid does.
NFPA 70E Section 120.3(D) Impedance states, "Temporary protective grounding equipment and connections shall have an impedance low enough to cause immediate operation of protective devices in case of accidental energizing of the electric conductors or circuit parts." ASTM F2249, "Standard Specification for In-Service Test Methods for Temporary Grounding Jumper Assemblies Used on De-Energized Electric Power Lines and Equipment," contains tables that give the maximum resistance for ground cables if there is any doubt that they are serviceable.
Safe Work Practices
There are a number of safety-related items that are not stated in either the OSHA regulations or the NFPA 70E. For safe use of personal protective grounding equipment, the following work practices should be observed:
- Never use components for personal protective grounds that are not sized or approved for that purpose. There are a zillion things that could be used, such as welding cables and clamps or automotive jumper cables, but when the short circuit current hits them, they vaporize or get blown off the conductor. The resulting arc flash will certainly damage equipment and could cause a fire, injury, or death to nearby workers.
- Use the grounding clamp that is designed to fit the type of bus or connection you're connecting to. As an example, don't try to use a clamp designed for tubular bus on a flat bus. It probably won't hold if there's a fault. And if you're thinking, "It will do for now," why put a ground on at all? If you're going to roll the dice, go for broke!
- Always test circuits for the absence of voltage before placing personal protective grounds. Just because you know it's de-energized doesn't mean that it really is. Both OSHA and NFPA 70E state that all circuits are to be considered energized until tested and proven de-energized.
- Always use live-dead-live testing when performing absence of voltage tests. Test the voltage detector on a known live circuit, test all circuits that should be de-energized, then retest the voltage detector on a known live circuit. I have had several voltage detectors go bad after the initial test. Following proper procedures, even when you are certain the circuit is dead, could save your life. Figure 3 is a sign at one utility's substation.
- Never, ever tap a circuit or device with a "static ground" to see if it is dead. Back in the day, I've seen electrical workers take a 12AWG wire and staple it to a broomstick handle. One end was connected to ground while the other end was stripped bare. The bare end was used to tap the "de-energized" conductor to ensure it was dead. This is another form of suicide by ignorance. If the circuit is still energized, the short circuit current will probably vaporize the wire, creating an arc flash that can injure or kill.
- Use as short a ground cluster as possible. This reduces the chances of the cable striking someone if it is accidentally reenergized and also reduces the overall impedance of the ground set.
- As stated earlier in this article, place grounds close enough to protect workers, but not so close that they will injure people nearby. When the short circuit current hits the ground cluster, it will whip around with tremendous force.
- Grounds must be placed using live-line tools. Never use hands, even hands in rubber insulating gloves, to place grounds. If there is an arc flash, you will be exposed to extremely high temperatures, well above what you may expect. This does not apply to static grounds used during testing power system equipment.
- If a ground set has "T" handles, it is to be used for static grounds only. They are suitable for use when a transformer or other piece of isolated electrical equipment must be grounded during an electrical test and can’t be subject to re-energization or fault-level currents. Always wear rubber insulating gloves when placing or removing static grounds.
- Wear proper arc-rated clothing and PPE when necessary. Yes, it is hot, it is bulky, it does make you sweat, and it also will keep you alive if there's an arc flash. Figure 4 shows a utility worker on his way to the beach -- or something.
Figure 4. Pass the suntan lotion, please!
- Never come into contact with grounds while they are being placed or afterward. The jacket on grounds is used to protect the fine conductors from being damaged, not as insulation. Don't step on them or reposition them using bare hands. The jacket would be of little use on higher voltage electrical systems.
- Inspect grounds before using them. ASTM F2249 provides guidance on the proper inspection and testing of ground clusters. Figure 5 is a common problem found on ground sets. In Figure 5, the cable is oxidized, the strands are exposed to damage, etc., etc.
Always track your ground sets when placing them on equipment or circuits. Every year, accidents are caused by grounds being left on when a system is re-energized. If sized and installed properly, the protective device should clear the circuit before substantial damage is done. Sometimes things don't go well, though. Shermco Industries uses the tagging system shown in Figures 6 and 7. Each ground set has a unique ID number that is stamped into a metal tag. That tag is attached to the ground set and to a removable clip. When the ground set is placed into service, the tag is unclipped from the ground set and locked onto the LOTO device, which also has a tag showing which circuit it is placed on. When the LOTO is released, the technician knows which ground has to be retrieved and where it is.
- If grounds are defective, tag them and remove them from service. Shermco uses the same tagging system used to identify each ground set to also track and inspect them for condition and testing. If the ground set is defective, that ID number is entered into the system, the grounds removed from service, and the grounds are repaired and tested or disposed of.
- Never stand near grounds that may be lying on the ground. If they are re-energized, they will try to straighten out with great force.
- Never coil grounds. If they are on carriers, remove the entire conductor from the carrier and stretch it out on the ground (earth). When short circuit current tries to pass through a coil of wire, the coil acts as an inductor or choke. Often the result is vaporized conductor.
- Inspect the grounds after using them. Take a few minutes to ensure they are still serviceable. Again, use ASTM F2249 as a guide for your inspection.
- Test personal protective grounds on a regular basis. ASTM F2249 states that grounds are to be tested at a "time interval established by the user to ensure that defective grounding jumper assemblies are detected and removed from service in a timely manner." It is the author's opinion that personal protective grounds are safety-related devices and, as such, should be tested annually.
Pacific Gas & Electric has tested various configurations of grounding clamps and has concluded that grounding stud/socket ground sets offer the lowest resistance and are easier to apply (when they can be used).
This is a very good addition during a shut down on a medium-voltage power system, as shown below in Figures 8 and 9.
Summary
Personal protective grounds are critical safety devices that require care and skill when using them. Improperly sized or installed grounds will only provide a false sense of security. Technicians often place personal protective grounds and don't give much thought as to whether they would actually protect them if the worst should happen. Once locked out and tagged, we have a tendency to consider electrical circuits and equipment "safe." Electrical circuits and equipment cannot be considered safe until tested and found absent of voltage.
If the system has a nominal voltage above 600V, grounding is a mandatory requirement. However, grounding is not just for high-voltage systems. If there is any danger of voltages appearing on the circuit or device, it must be grounded. UPSs, VFDs, and similar types of equipment have large capacitors that can store a lethal charge. Backfeeds through light circuits or CPTs can also be issues. If there are de-energized cables run for long distances in cable trays that contain energized cables, an induced voltage can appear on them. Proper grounding and grounding equipment that meets ASTM F2249 and ASTM F-855 specifications is necessary to provide a safe work environment.
This article originally appeared in the June 2013 issue of Occupational Health & Safety.