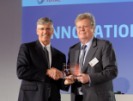
Gas Monitoring Success Stories
Wireless gas detection is a cost-efficient way to improve safety.
When a multinational energy company wanted to improve plant safety by expanding its area monitoring for toxic gases at a large petrochemical and refining facility, the facility’s top safety manager did what he always did: He got an estimate for trenching and running miles of underground cables out to the area to be monitored.
“While my first instinct was to install fixed monitors throughout the tank farm storage area, the initial cost estimates were very high for running cables. This quickly put me on the path to finding an alternative solution,” said Alan Brown, health supervisor and industrial hygienist for the Port Arthur Refinery of Total Petrochemicals & Refining USA, Inc. The path led to Brown’s developing the world’s first automated and permanent wireless gas detection system.
The Total Petrochemicals & Refining system integrates radio frequency (RF)-enabled gas detection monitors and uses intrinsically safe solar power and plume-modeling software. The wireless system was designed with the help of several companies in the safety field and now provides continuous monitoring for hazards such as hydrogen sulfide (H2S) and sulfur dioxide (SO2) at the facility’s tank farm. The wireless system also monitors tanks a few miles away. “We saw a significant cost savings on this project by going with a wireless solution instead of a fixed-wired approach,” said Brown, who received company accolades and an award for his innovative approach to enhancing safety at the plant.
Why Wireless Gas Detection?
Wireless gas and radiation detectors can be used in a wide range of industry applications, including oil and gas refining, chemical production, coal-fired power production, and rendering plants. With wireless gas detection, if an incident happens, alarms immediately alert area workers and the monitors send alarm information to a command center operator who can initiate an emergency response faster than ever before. Plant operators also can be alerted in real time about man-down alarms or excessive biometric vital signs of team members in stressful or potentially hazardous environments, and plant managers can consult with experts in other locations or share data in real time with key stakeholders via the Internet.
Using wireless gas monitoring, data are sent over the air in real time to dedicated monitoring computers, which can be located on site or at an off-site facility. The data can be captured and stored digitally with GPS (global positioning satellite) location coordinates, time stamp, and concentration data to document incidents and confirm adherence to regulations. Hand-held and personal monitors can utilize wireless modems to connect seamlessly to a wireless monitoring network.
Advanced software adds functionality to wireless gas detection systems. Real-time instrument monitoring, management, and control software provides support for continuous operation. This software provides the ability to remotely track hundreds of wireless monitors at one time and aggregate readings from multiple locations into a dynamic map display. This gives safety managers insight into threat conditions and greater control of their threat data to provide the safest environment possible.
At the Total Petrochemicals & Refining plant in Port Arthur, Brown’s goal was to implement around-the-clock wireless monitoring of about 100 storage tanks. These tanks contain potentially explosive chemicals with low LELs (lower explosive limits). The monitoring solution needed to track leaks, overfills, or other hazardous conditions that could cause an explosion if the combustible gases found an ignition source.
Brown combined the expertise of three companies to develop a low-cost, low-maintenance wireless monitoring system. A local company developed a weatherproof enclosure – capable of withstanding hurricane-force winds – to house a wireless multi-gas monitor and a solar-powered energy source to eliminate the need for battery maintenance. To meet strict Class 1, Division 2 intrinsic safety requirements, the gas monitor manufacturer developed a safe connector to link the monitor’s battery to the solar panel. The system is certified as intrinsically safe in the United States and capable of powering a multi-threat monitor for up to 14 days without sun, Brown said.
The final element of the system was integrating the wireless monitor’s data with the facility’s two meteorological stations and its plume measurement and modeling software. The decision-support software estimates downwind concentration levels and models the direction and altitude of a release in real time.
“I am a big proponent of wireless technology and the capabilities it brings to providing and enhancing safety in industrial environments,” Brown said.
Flexibility and Scalability
Another wireless gas detection success story is found at a Southeast U.S. chicken-rendering operation where H2S gas was a challenge to workers. System flexibility and plant safety were key concerns for its general manager.
H2S is a highly toxic gas produced through the natural decay of organic materials. Aware that safety violations for putting workers at risk could result in significant government fines or the loss of life, as occurred at a chicken plant in Arkansas in 2003, the general manager chose a wireless gas detection solution to avoid the difficulty of drilling extensive holes through the facility’s concrete walls to run the cables needed to install fixed monitors. The system was installed by TekSolv, a Newark, Del.-based company that provides safety and gas detection services to its clients.
TekSolv Sales and Business Development Manger Michael P. Ryan said wireless systems have been cost-efficient solutions for several clients. A refinery deployed one as a temporary replacement for an aged, degraded, fixed system that monitored the facility’s crude unit. The refinery’s safety manager liked the wireless approach so much that he purchased the system, replacing the fixed-wired system with a fixed-wireless solution that provides real-time data to a control room computer. “Swapping out the fixed-wired system would have cost them a lot of money in man-hours to run wires and conduit,” Ryan explained. “While wireless solutions have not traditionally been thought of as a permanent, fixed-monitor solution, we are seeing more of our customers go that way.”
The refinery maintains a very clean and controlled environment, and cable-free gas detection helps to keep it that way, he said. The wireless gas detection system offers portability, allowing personnel to relocate the system easily to different production areas of the plant where safety threats exist.
Beyond the cost savings, many industrial safety managers see other advantages to going wireless, including the elimination of exposed wires and cable harnesses. Additionally, wireless systems are more scalable than their fixed counterparts, Ryan said. At one refinery, a fence-line monitoring system was easily reconfigured with no rewiring required when the footprint of the site changed. “Wireless detection applications today have a proven track record for delivering new functionality and unmatched safety improvements,” Ryan said. “These systems are making an impact by raising safety and reducing the overall cost of detection monitoring.”
This article originally appeared in the October 2012 issue of Occupational Health & Safety.