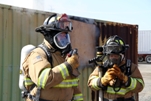
Prevention and Readiness at Clearwater Paper
With an average of 250 fire calls each year, quick response is vital to keep fires from spreading, says Brad Hukreide, fire chief at the Lewiston, Idaho, paper mill.
- By Kate Woldhuis
- Jun 01, 2012
Anyone who has been in an emergency can tell you that a person's response is based mostly on instantaneous reaction and thought. This is why emergency response training is essential for all employees: so an employee's thoughts and reactions in an emergency are based upon previous practice and learned behavior.
Consider a paper mill, for example. One can imagine how a small fire at a paper mill could quickly become out of control, not to mention the inherent occupational dangers that come with lumber and pulp processing. Imagine large metal saws that process lumber and spew sparks around large piles of sawdust on the ground, employees working at high angles and in confined spaces, employees doing heavy lifting and utilizing hazardous materials, and lumber piles several stories high and football-field-lengths long that, given the right conditions, could spontaneously erupt into fire. Even under the most stringent safety program, occupational and fire hazards can abound in such environments. Because of all this, members at the Clearwater Paper Fire Department (CPFD) in Lewiston, Idaho, have developed their emergency response plan with prevention, preparedness, and training as the first line of defense against emergencies.
Given the dangers and the mill's large size and somewhat rural location, Clearwater Paper has had an on-site fire department for more than 30 years. Located next to the Clearwater River, the Clearwater Paper campus is essentially its own little community with its own power plant, fire and medical facilities, water treatment plant, and production area. CPFD is on hand during all shifts to oversee confined space and high-angle work, conduct fire watches, perform maintenance of fire hoses and extinguishers, and hold fire safety and first aid education for employees and contractors on site and other training programs for employees. It also does community outreach, teaching fire safety at schools and day care facilities.
The fire department operates three shifts that provide 24-hour coverage Monday through Friday. Even though each firefighter maintains EMT-level certifications, working in conjunction with CPFD is an on-site first aid clinic. Both the clinic and the department are operated by Medcor, a work site health services firm headquartered near Chicago.
The clinic is staffed with four nurses who operate the clinic around the clock on weekdays. The clinic's staff provides immediate response to occupational injuries and illnesses, as well as conducts fitness-for-duty exams, employee drug screenings, health and wellness checks, and much more to keep employees safely on the job and productive.
Much of the staffers' focus is on prevention. Covering a sprawling, 990-acre campus, they routinely perform drive-abouts to watch out for fire and safety hazards. They also perform walk-throughs of all buildings on the campus. These are critical components to prevention; both the clinic staffers and the firefighters are able to see the employees performing their job duties and any hazard that is present. In this way, they support Clearwater Paper’s safety staff by enforcing corporate safety guidelines and making safety observations if necessary.
Hazard Analysis
Several incipient fires, as well as some health-related emergencies, have been caught early on during walk-throughs and drive-abouts. "We have an average of 250 fire calls each year," said Brad Hukreide, fire chief at CPFD. "While most of those calls are for fires that are incipient, it is crucial that there is a quick response to prevent that fire from spreading, because it will spread quickly."
During September 2009, 106 incipient fires erupted at once in a lumber pile that was five stories high and 500 to 600 yards long. Despite CPFD's quick response to the fire, it took 18 hours for three fire departments to extinguish the fire.
Prevention efforts greatly minimize hazards but don't eradicate them. Therefore, another component of developing a comprehensive emergency response plan is preparedness. This element starts with safety and risk managers who mitigate work site risks in order to minimize the potential for disasters and minimize the potential impact of a disaster should one occur. This takes careful thought and planning and requires a comprehensive analysis of each employee's job tasks: What risks does each job entail? Are employees using their personal protective equipment properly? If a fire hazard is present, is there an extinguisher close by? Is there an eyewash station near employees who use chemicals?
At Clearwater Paper, employees can face risks of confined space entrapment and also high-angle dangers. All firefighters at Clearwater Paper are trained on site in high-angle and low-angle rope rescues and in confined space rescues, which is training that is not often available for most municipal firefighters. Firefighters who have this training are stationed throughout the buildings or are called to specific areas on campus to monitor employees working in confined spaces, at high angles, or when there is a high risk of fire. For all high-/low-angle or confined space work, firefighters work with employees beforehand to devise a plan to minimize risks while carrying out their duties.
Along with the clinic staffer, the firefighters train employees to perform CPR and use AEDs and fire extinguishers when needed. They also perform pre-employment physicals and monitor medical surveillance programs and spirometry testing. Employees must enroll in an annual incipient fire class where they learn and practice using fire extinguishers and fire hoses. (There are more than 2,800 fire extinguishers and 8,000 feet of fire hoses located throughout the campus.) They also learn to determine when it's appropriate to utilize the fire extinguishing equipment and how and when to call fire response.
Drills and Contractor Training
This training is reinforced with routine evacuation drills that ensure employees are up to date on safety and emergency response protocols and are prepared to carry out their tasks in the emergency response plan. Each division of the paper company runs one evacuation drill per year for each of the four shifts. The fire department and on-site clinic participate in the drills. Staffing is doubled at the clinic and the fire department during the drills so personnel are available if a real emergency occurs. For drills that do not require emergency response, members of the fire department observe the drills and provide feedback.
Contractors that are on site are trained according to the facility's safety and emergency response guidelines. Once per year, the entire plant shuts down for 10 days and 1,200 extra contractors and staff members are on site to perform all major machine fixes and cleanouts. Due to the additional staff and the nature of the work, first aid staff at the clinic and response teams at CPFD are doubled to provide complete coverage.
Setting Up Your Emergency Response Team
Just as wind can quickly spread a fire, an untrained employee can cause undue damage to a property or a person. Although not every facility has dangers equivalent to those of a paper mill, following the example set by the members of the Clearwater Paper Fire Department and the site's first aid clinic will provide great value when training employees on effective emergency response practices:
- First, analyze each employee's job duties, and then devise prevention protocols that are based on careful analysis of the work site job tasks and hazards. Ask employees what they consider to be their most risky job tasks and develop a comprehensive response plan that is easy for employees to remember and execute.
- Next, designate an internal emergency response team (its size should depend on the size of the facility) and train those employees on the facility's emergency protocols. Choose people who are confident, willing, and able to respond in case of an emergency. In their roles on the emergency response team, they are never to put themselves into dangerous situations; they must be trained on when it is appropriate to provide response and when to get out and call for help.
- Lastly, coordinate with local or on-site emergency response teams to ensure your emergency response and preparedness plans are both comprehensive and effective. Coordinate with them before the next disaster drill. It will add value to the facility's emergency response plan and allow them to become familiar with the site, its hazards, and the emergency response team members and protocols. On an annual basis or more often if you deem it necessary, update the emergency response protocols, hold regular safety meetings with staff to update them on all changes or improvements, and then enforce that training with regular disaster drills.
This article originally appeared in the June 2012 issue of Occupational Health & Safety.