The Index Enigma
Understanding the different text and performance PPE standards in use around the world will help safety managers apply them
- By Giovanni Henssen
- Apr 01, 2009
Today, the development and manufacturing of safety gloves is a global industry. Gloves are made and sold all over the world to multinational companies that operate in different countries. 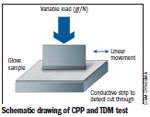
Determining the level of hand protection performance required in a safety glove is critical to the right glove specification. However, different standards and different test methodologies are in use, which can be confusing and complex for safety managers. It is imperative that buyers and safety managers of gloves seek out expert advice and counsel to help them make sense of the different and often incomparable data available.
In the first of a two-part series, this article sets out to describe the various test methods and performance standards available for
hand protection that are currently being applied in different regions around the world. It highlights the key differences between the standards and explains why it is important that safety managers, workers, and buyers understand how the differences can affect their choice of glove, the safety of their workers, and, ultimately, their bottom line.
Three Different Testing Standards
Today, there are three different standard cutting methods in use around the world.
The ASTM F1790-05 Test Method For Measuring Cut Resistance of Materials Used In Protective Clothing is a North American standard, published in 2005, which supersedes ASTM F1790-97, (published in 1997).
The second test method is the European standard EN388 Gloves Giving Protection from Mechanical Risks. Although this is a European standard, it is recognized in other regions worldwide and is becoming more apparent in North America.
The third method is the international standard ISO 13997: 1999 Protective clothing— Mechanical properties—Determination of Resistance to Cutting by Sharp Objects. This standard is used in all regions of the world.
Three different test methods are described by each of these standards for measuring the cut resistance of safety gloves. The test standards, methodologies, and where they are used are set out in Table 1.
Test Methods and Procedures ASTM '97 and '05
The ASTM test measures the amount of pressure that can be applied on a straightedged blade, while moving the blade over the fabric of the glove, without cutting through the fabric for at least 0.8 inch (20 mm). This simulates a cut or slashes with a sharp object. The ASTM '97 standard describes the CPP method, while the newer version, the ASTM '05, also describes the TDM 100 method that was introduced to try to correlate with the ISO 13997 standard.
ASTM '05 also describes a new procedure for carrying out the test. Although it allows either the CPP or the TDM 100 to be used to carry out the test, it only permits the new procedure to be used. The differences between the testers and the procedures are extremely important to appreciate, as we shall discuss in the next paragraph.
The procedures detailed in the 1997 and 2005 versions of ASTM differ in at least one important way: In the 1997 version, the glove fabric is placed over a piece of tape, and the blade has to cut through both the fabric and the tape; in the 2005 version, a copper strip is used between the glove sample and tape so that when the blade cuts through the fabric and touches the strip, an electrical circuit is completed, indicating the end of the test. So the '97 method measures the cut performance of the sample including the tape, while the '05 method measures only the cut performance of the glove sample. The '05 method provides a more accurate picture of the cut resistance of the glove, and in fact the results it yields are slightly lower than with the '97 test.
EN388
The European standard EN388 was first published in 1994 and revised in 2003. The Coup test method describes a totally different principle from the CPP and TDM method. In the Coup test, a circular blade moves back and forth across the sample under a fixed load of 500 g while rotating in the opposite direction of the linear movement.
ISO 13997
The ISO 13997 standard was the first standard to specify the exclusive use of the TDM 100 tester, which is the same as the ASTM '05 method. No other tester device is allowed.
Performance Standards
ANSI/ISEA
There are also two different performance standards that provide ratings from 0 to 5 according to how gloves perform in the cutting tests. The U.S. standard is ANSI/ISEA 105, American National Standard for Hand Protection Selection Criteria. This was developed by the American National Standards Institute (ANSI) and the International Safety Equipment Association (ISEA), the U.S. trade association. Glove performance and pass/fail criteria are provided not only for resistance to cutting, but also to puncture and abrasion, chemical attack, heat, and flames.
ANSI/ISEA 105 provides a numeric classification of cut resistance (see Table 2) from 0 (least cut resistance) to 5 (most cut resistance), but it is still based only on results from the old ASTM '97 standard. It is important to realize that these performance levels are different from the results obtained under ASTM '05 or ISO 13997.
EN388
The European performance standard is incorporated in EN388, which also covers a variety of safety aspects. Under EN388, the result of the test on the glove is compared to the resistance of a reference cotton fabric. The Cut Index indicates how much better the sample is compared to the reference cotton fabric (see Table 3). For example, a cut index of 5 means the sample has five times better cut resistance than the reference cotton.Because the blade loses some of its sharpness during the test, this method is not very suitable for testing highly cut-resistant gloves. For those types of gloves, the EN388 standard recommends testing according to the ISO 13997 (TDM) standard.
Another very important difference between EN388 and the other test standards is that EN388 describes not only the cut resistance of a glove, but also the abrasion, puncture, and tear resistance. All four properties are linked to each other:
Abrasion resistance. Low abrasion resistance of a glove has a negative effect on the consistency of the cut protection in use, significantly shortening the lifetime of the glove.
Puncture resistance. Low-puncture-resistant materials (typical for sting knit gloves) will perform better if they have a higher tear resistance.
Tear resistance. If a glove is compromised from a puncture, having a high tear resistance will prevent the glove from tearing and ultimately protect the wearer from a laceration.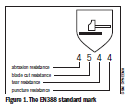
The EN standard mark lists the individual performance levels for abrasion, puncture, and tear, as presented in Figure 1.
Within the European Union, protective gloves that are classified as personal protective equipment must be CE marked to indicate they meet specifications as described in the EN388 2003 standard. A glove can be CE marked together with the EN388 logo only when all the tests have been performed by a notified laboratory, giving performance levels for each property that has been tested.
Understanding the Differences
The various standards differ, and results from the different tests generally do not correlate with one another.
Results obtained with both CPP and TDM test under ASTM '05 are similar; however, results obtained using the CPP test under ASTM '05 are not comparable with those carried out using the CPP tester under ASTM '97.
Results carried out using the Coup test in EN 388 do not correlate with any other method.
Even more important are the differences in the performance standards. As previously noted, EN388 and ASTM both use numeric classifications to indicate the level of cut resistance of a glove (see Tables 2 and 3), but there is no correlation between the classifications. Buyers need to understand where their actual glove requirement fits within this range and should not simply be specifying a certain cut level. Gloves with two different performance levels can be very close in actual performance. For example, a Level 3 glove at cutting force 1,498 is practically identical to a Level 4 glove of 1,502 cutting force.
This situation can obviously add confusion for end-users trying to select the right glove for their application. It is important for them to understand the differences between these standards and the test methodologies specified in them, in order to set the right expectations for performance and specifications. In summary, they should understand that:
CPP/TDM indicate how much force (load in grams) is needed to slash/cut through a fabric.
Coup test indicates how many repetitive cuts on the same position are needed to cut through.
EN388 cut level X (Coup test) does not correspond to the same ANSI/ISEA 105 level X (ASTM '97).
CPP values measured with the ASTM '97 indicate higher cut resistance than the ASTM '05 and TDM tests on the same glove.
Minimizing Confusion
Safety managers will specify the type of glove they need. A company making razor blades is naturally going to demand a glove with higher cut resistance than a company working with less sharp objects, but it still remains at the discretion of the buyer as to which glove they buy; there is no law telling them they must use gloves conforming to any particular standard. So end users are in many cases dependent on their contacts at glove companies and distributors to make sure they get the right level of protection. Manufacturers and sellers therefore play an important role in the correct specification of gloves.
In principle, the U.S. Occupational Safety and Health Administration's general duty clause stipulates that employers must provide employees with adequate protection for the hazard, but it does not specify what the adequate protection should be. This could expose employers to liability where, for example, they unwittingly procure gloves that have a lower actual performance level than gloves previously used. This is why safety managers need to be informed on how to properly interpret the data from the different standards and performance levels in order to make educated decisions.
Safety managers should build relations with their suppliers who have expertise and knowledge in hand protection. The suppliers should be aware of the global variations in standards relating to their performance and be capable of providing the correct advice on the right glove for any specific job that is carried out in any specific environment. The cut resistance performance level numbers are only a guideline and, as described previously, are not compared from one standard to another. Obtaining good information from reputable companies coupled with expert advice and guidance can help buyers make sense of the information and make the right decision. Only in this way can the safety manager be confident the employees are obtaining the level of protection that they require.
This article originally appeared in the April 2009 issue of Occupational Health & Safety.