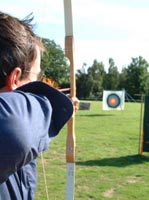
Accomplishing Your Long-Range Goals for Safety
Admit it: All of us want a model safety program worthy of our talent, efforts, planning, and management ability. We begin each cycle, whether quarterly or annually, with a plump list of programs and specifics to create the perfect safe working environment. Then, the reality spheres of time, cooperation, and funding set a collision course with our goals, and before we realize it, time has flown by and we are no closer than before. So the question is; how do we accomplish our long-range goals for safety?
Set goals, both long range and short. I have a laundry list of what I want our safety program to be in five years. I also know what our shortcomings are today. So I have three lists:
• One consists of long-term goals of a programmatic nature.
• The second list is short-term (3-6 months) goals, usually within one program that deals with specific hazards.
• The third list is for equipment and training needs.
Once you have these on paper, you can start working with the sections of each goal. Break each goal into parts that are "doable." One small task is easier to handle and finish than starting a new program from concept to completion at one time. Be realistic on funding and assistance. Funding usually is forecast years in advance, with small increments of increase. I typically "pad" my budget requests every year to include unexpected situations or new program implementation. I also always request assistance for seasoned office support to keep me organized (or try to, at any rate).
Also, throughout the year, if I save funds, I advise upper management (in writing) how much I saved and how I put the money to critical use. Never allow funds to sit and wait. Unfortunately, they will be scarfed up by another in the budget group.
How to Get Help
Ask for help. (You never know, this time you may get it!) Request help in a short-term format, such as a temp. Ask for any "light duty" personnel with skills you can use. Also consider using enthusiastic employees, safety committee members, and university grad students who need work credits. When using temp help such as this, make sure the tasks are well-defined, short-term items. This avoids allowing the project to fall or short of completing or be dropped.
Keep the goals list in front of you. I even add these items to my calendar at varying times to "jog" my memory and keep me moving forward on these worthy items.
Work on elements that are important to the program overall! Also, consider what is really needed. Resolution of physical hazards takes priority over paper chases, in my opinion.
Each goal has an expected outcome and impact on the company. Make sure you keep upper management advised on your impact, both good and bad, on production. Planning means everything here; shutting down half the workforce for training in the busiest time of year may not be the best course of action. Think in terms of options!
We get so mired down in the mud of day-to-day safety activity that we tend to let time escape all too quickly. Your corporate management wants accountability in all areas, so when providing goals and objectives at the beginning, be kind to yourself. It is better to have only three to five goals that you will accomplish than to provide 30 and have just six accomplished at the end.
Safety goals are like a big jigsaw puzzle: Many small parts must be completed to see the big picture. As safety professionals, we must keep the work forever moving forward, even though we'll move faster at some times than others. You can do it! On our success depends each employee's life/workplace safety.
About the Author
Linda J. Sherrard, MS, CSP, is Safety Consultant II with Central Prison Healthcare Complex, NCDPS in Raleigh, N.C., and is the former technical editor of OH&S.