Your Forklift Safety Zone
Advances in forklift and pedestrian safety alert technologies can markedly reduce accidents.
- By Kenneth Lawrence
- Feb 01, 2007
FORKLIFT
trucks are an essential part of most industrial and supply chains
around the world. However, statistics indicate they also present a very
significant hazard to people occupying the same workspace.
Forklift-involved injuries can be severe or fatal because the trucks
are heavy and powerful vehicles.
Twenty years ago, the forklift was a major cause of industrial
deaths and accidents. Unfortunately, little has changed, until now.
This article will explore new forklift and pedestrian safety
products that are being hailed by some as the most exciting piece of
occupational health and safety news for decades. The products are truly
revolutionary and offer a new breakthrough in detection technology and
are making a strong impact in safety applications.
Forklift Accident Statistics
As reported by the National Institute for Occupational Safety and
Health in June 2001, forklifts strike pedestrians every day and result
in 100 deaths and more than 20,000 injuries annually in the United
States alone. The NIOSH report shows that approximately every three
days, someone in the United States is killed in a forklift-related
accident. Each year, an additional 94,750 injuries related to forklift
accidents are reported. The costs incurred because of forklift
accidents are estimated to be above $100 million.
How do we get to such a large number? Besides worker's compensation
or workers' lost time at the job, there are huge lawsuit awards made
for forklift accidents. When you start adding up awards such as
$750,000 for a back injury or $2.8 million for a foot injury, it's easy
to see how these costs add up, given the number of incidents reported
each year.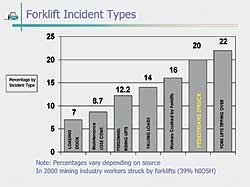
Forklift accidents happen for many different reasons. The chart
below shows accident percentages based on incident types. The first
four safety alert technologies described in this paper will focus on
the second-leading forklift incident type, where forklifts strike
pedestrians.
Safety Alert Technologies
There are numerous technologies being developed today to address
safety issues for industrial applications. Four technologies discussed
here can help to reduce the incident rate of pedestrians being struck
by forklifts; another technology helps reduce accidents by using
preventive measures that include maintenance and training awareness.
1. First is a proximity laser scanner that mounts on the
front or back of a forklift truck and provides warning and safety zone
areas for safeguarding and collision avoidance for mobile vehicles. The
scanner can designate a slow-down area (warning zone) and stop area
(safety zone) within the scanner's range.
Typically used on automated guided vehicles, there is no reason this
safety-rated laser bumper can't be used on a forklift to help
distracted operators avoid serious collisions with pedestrians or other
vehicles. When a person or object is detected, the laser scanner can be
configured to govern the forklift speed to slow down and can trigger
lights or audible alarms warning the operator before an accident
occurs. With onboard sensor technology, forklift drivers can reduce
product and vehicle damage while helping to prevent accidents.
2. Another system to alert pedestrians or other vehicle
traffic of approaching forklift trucks coming into an intersection uses
a microwave motion sensor that detects only vehicle traffic in the
sensing area. Once this is detected, the controls lock in as long as
the forklift is moving toward the center of the intersection. Audible
and visual alarms are engaged until the vehicle has fully passed
through.
The system automatically resets and awaits the next forklift. As a
result, pedestrians and other forklifts are alerted to oncoming traffic
so they can react in a timely manner and avoid contact with the
approaching forklift. The unit is self contained and typically is
installed over busy forklift intersections that may also include
pedestrian traffic.
This unit works well in an open warehouse operation where the only
support structure to hang and power the device is the ceiling.
3. An innovative, infrared communications technology consists
of a vehicle-mounted transmitter beacon and wall-/door-mounted
detectors. An invisible 30-foot beam sweeps around the forklift truck
whenever it is operational. Strategically placed receivers detect the
vehicle's proximity and activate warning systems (via zone controller),
such as flashing lights, physical barriers, audible alarms, signs, or
door locks.
The technology is not based on radio frequency (RF), so is not
affected by interference from other plant or passing equipment. A long
detection range and a configurable detection zone ensure vehicles are
accurately detected on approach from any direction or orientation.
This system gives an early, specific warning that a forklift is
approaching in what may otherwise be an area where the forklift is not
yet visible, such as blind corners, doorways, around machinery, etc.
4. Accident prevention is universally desirable. By
automatically tracking the movement of forklift trucks, a fourth system
knows each vehicle's location, heading, and speed in real time. This
information can be utilized to warn pedestrians and vehicle operators
of potential collisions and other dangers. Knowing precisely where
vehicles are located at every moment, this system can signal nearby
pedestrians and other vehicles equipped with the technology before
collisions occur.
This system monitors vehicle locations and transmits messages to the
traffic control system upon a vehicle's entry into a Caution zone or
Danger zone. Traffic control signal lights or audible horns at
intersections alert oncoming forklift vehicles or pedestrians to
approaching vehicles. Control of all intersections can be maintained
with a single traffic control system.
5. The fifth technology in our discussion involves fleet
management systems that provide preventative maintenance and training
certification monitoring that can help avoid another 20+ percent of
forklift incidents that pertain to poorly maintained forklifts or
untrained operators.
One manufacturer offers a modular system that includes keyless
access control, ensuring only authorized operators with current
training credentials can operate the forklift. By eliminating the need
for a key, unauthorized access to the equipment is eliminated.
The LCD display module automates a daily OSHA safety checklist that
is customized to ensure strict compliance with OSHA regulations for
vehicle safety inspection. This system will provide automatic lockout
and generate a maintenance work order to ensure safe operation of the
vehicle.
The impact shock sensor is easily programmable for shock levels and
records the impact severity to identify and train abusive drivers.
Real-time audio and visual indicators provide immediate feedback to the
driver, while impact data is transmitted via an RF communications link
to the reporting system.
With the standard reports and charts packages, companies can analyze
their forklift fleet utilization, driver productivity, task efficiency
and activity metrics. Training coordinators can be alerted when driver
certifications are about to expire and can manage vehicle access based
on certification. Maintenance managers can monitor impact data and
manage maintenance schedules via the electronic recordkeeping recorded
from the OSHA safety checklist.
Creating a Safe Working Environment
Some companies have the ability to separate forklift and pedestrian
traffic by keeping forklifts out of areas used by employees or using
guarded walkways, painted aisle, or strategically placed signs. In the
cases where improvements are needed to reduce forklift and pedestrian
collisions, technology can play a significant role.
Companies can zone critical pedestrian and vehicle intersections by
picking safety alert technologies that fit their needs. Reductions in
abuse and damage by enforcing driver training certifications and using
paperless reporting systems while providing management with better
tools will help to create a safer work environment.
This article appeared in the February 2007 issue of Occupational Health & Safety.
This article originally appeared in the February 2007 issue of Occupational Health & Safety.