Innovative Field Practices in Hearing Conservation
Four companies share the strategies they use to redefine success.
"WE'VE got twenty-five years of audiometric data that shows what we're doing in our Hearing Conservation Program doesn't really work." I couldn't believe my ears. The safety manager at this large company administered a totally compliant OSHA-standard Hearing Conservation Program. Everything had been in place for more than two decades: noise monitoring, audiometric testing, hearing protectors, annual training, and recordkeeping. But the number of recordable hearing losses continued climbing steadily.
It is a sentiment echoed in many noisy companies, both large and small. Employers invest the time and money to administer an OSHA-standard Hearing Conservation Program with the expectation that providing ear plugs should stop hearing loss. But the false expectations are dashed when recordable hearing losses continue occurring and claims for noise-induced hearing loss continue unabated--or, worse yet, climb higher.
How does a safety manager take hearing conservation to the next level, from a hearing loss documentation program to a hearing loss prevention program? Safety and industrial hygiene professionals at four companies discussed with us how they changed their practices to make their Hearing Conservation Programs a preventive force in their companies' safety strategies.
Company 1: California Manufacturer
By all appearances, this manufacturer with 120 employees was doing everything right. Employees watched a motivational training video in groups prior to their annual audiometric testing. The video contained all the OSHA-required elements: the effects of noise on hearing, the purpose and use of hearing protectors, and the purpose and procedures of audiometric testing. "But we walked onto the production floor an hour later and noticed the same 'trained' workers with ear plugs barely inside their ears," lamented the contracted audiologist. "Those ear plugs were doing nothing more than looking good--they were not functional at all. We had to try a different approach."
The safety manager pulled the plug on the annual hearing conservation video shown to groups of noise-exposed workers ("We would have employees tossing paper clips during our group sessions") and replaced the group training with a one-on-one review of each employee's audiogram and fit testing of hearing protectors. The results were embarrassing and enlightening. "We had workers who had participated in years of group training and yet were unable to properly fit their foam ear plugs--it had never been required of them. We even had managers who failed our proper-fit check." The new one-on-one training format required every worker to demonstrate a proper fit--no exceptions.
Studies repeatedly confirm the advantage of one-on-one training and personal feedback in preventing hearing loss. For noise-exposed workers, that training is most effective when offered in conjunction with audiometric testing. Lower rates of hearing loss have been documented among employees who receive a copy and explanation of their audiometric results, compared to their co-workers who received no feedback. One research study has documented an average 14 dB increase in the measured protection of ear plugs when workers received just two to three minutes of one-on-one training in proper plug fitting. Another study found significantly better fit and attenuation of ear plugs when training was administered individually as opposed to groups.
TIP: Use one-on-one training to focus on proper fit. Document that each employee can demonstrate a proper fit. Make sure every supervisor knows how to properly fit the hearing protectors and how to check visually for proper fit in workers.
Company 2: Aerospace Manufacturer
Something didn't sit quite right with one safety manager when he reviewed his hearing conservation training materials: The examples of noisy equipment were all occupational. He knew his workers were exposed to hazardous noise at work, but he also knew they had some very high non-occupational exposures. "We adjusted our training to focus more on the off-job hearing protection. For workers in our region, we call them 'the big three'--power tools, chainsaws, and firearms." By using the workplace training to focus on non-occupational hearing protection, managers were bridging the gap for workers to carry over their hearing conservation practices from job to home.
"We also encouraged--not just allowed, but encouraged--our workers to take their hearing protectors home." And years after that take-home policy was initiated, there have been zero concerns or complaints about employees abusing the free ear plugs.
Workers who comply with all hearing protection requirements at the workplace may revel in noisy recreational activities off the job. And because OSHA-required audiometric testing does not differentiate between occupational and non-occupational noise-induced hearing loss, employers may be stuck with the responsibility for those off-the-job hearing losses when they show up in future audiometric testing.
The ears do not operate on a time clock: a 95 dB exposure at work is just as hazardous as a 95 dB exposure listening to loud music in the car, running power tools in the garage, or operating the lawnmower or edger in the yard. Unlike work, there are no posted warning signs for these non-occupational exposures. But the need for protection is just as critical to good hearing, whether on the job or off.
TIP: Encourage workers to use their hearing protectors for off-the-job exposures. Employees should be familiar with the rule of thumb for identifying hazardous noise: If you must shout to be understood by someone standing an arm's length away, then that background noise is probably hazardous (85 dB).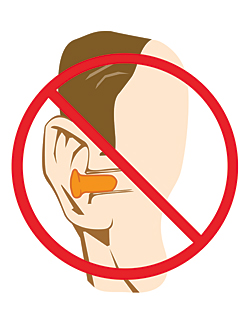
Company 3: Metal Fabrication Shop
Since the 1980s, hearing conservation procedures had been in place at this facility. "That was kind of the problem," says the safety manager. "We were in a hearing conservation rut. We were going through the motions without seeing any success or even knowing how to define success in our program." When managers stepped back to assess the program, they realized success could only be defined one way for them: zero percent recordable hearing losses.
Their first step was to revisit their noise control options. A Hearing Conservation Program for noise-exposed workers is not the first line of defense against hazardous noise; eliminating noise hazards at their source is the only sure method of preventing workplace hearing loss. Complete noise control is sometimes not feasible, but many engineering solutions are very cost-effective when compared with the ongoing expense of recordable hearing losses.
By contacting vendors and equipment suppliers to explore updated noise control features, the fabrication shop was able to reduce noise levels significantly, thus requiring fewer employees to be monitored in the Hearing Conservation Program. While noise control solutions vary significantly for each work process, successful reduction of noise often involves a combination of "Buy Quiet" policies, retrofitting existing machinery, erecting barriers to block noise, or isolating noisy equipment to a protected area.
To reach their goal of zero percent recordable hearing losses, shop management chose another solution for the remaining noise-exposed employees: fit testing of hearing protectors. (Several field verification methods such as fit testing are summarized in the June 2006 Occupational Health & Safety article "Fit Testing Ear Plugs," on page 38.) Using this procedure, workers are given a specialized hearing test while wearing their ear plugs, then repeat the test without the ear plugs. The difference between the two hearing tests essentially tells us how much protection was achieved by the user in real-world usage.
Fit testing of hearing protectors makes the common estimation method (the Noise Reduction Rating) mostly obsolete. The NRR is a laboratory evaluation method used to estimate noise protection, but it is a poor estimator of a hearing protector's performance on individual users. Fit testing now allows safety managers to measure, not just estimate, the amount of protection a particular worker attains with his/her hearing protectors. Not all workers will achieve an adequate fit with all ear plugs, and fit testing is the best available tool to measure those differences. One facility places color-coded stickers on the hard hats of workers who have "certified" proper attenuation with their ear plugs.
TIP: Do not assume the noise is insurmountable: Reconsider engineering solutions to reduce the number of exposed workers. For noise-exposed workers, use fit testing to ensure adequate real-world protection is being achieved.
Company 4: Foundry in the Northwest
Many companies pull the OSHA-required components of their Hearing Conservation Program off the shelf annually, dust them off, and replace them on the shelf until next year's audiometric testing and training. But some companies essentially perform noise monitoring and training daily on every noise-exposed worker!
The feat is accomplished using in-ear dosimetry developed by Dr. Kevin Michael. Using this device, miniature microphones are inserted into ear plugs or ear muffs and connected to a pocket-sized noise dosimeter worn by the worker. The dosimeter continuously monitors the noise level under the hearing protector and immediately warns of any noise measurement exceeding action levels. The device also integrates the noise levels throughout the day to provide a total-shift readout of the time-weighted average exposure. If hearing protectors are worn properly, the in-ear dosimetry will confirm noise levels less than 90 dBA (or 85 dBA if the worker has already demonstrated an OSHA-defined shift in hearing). If hearing protectors are worn improperly or removed for a significant amount of noise exposure during the work shift, the dosimetry will confirm over-limit exposures.
The training effect of in-ear dosimetry is substantial. Workers receive immediate visual feedback if their noise exposures are over-limit, and they can also see the detriment caused by removing hearing protectors, even for a few seconds, to talk with co-workers or listen to machine sounds. In extreme noise environments, in-ear dosimetry confirms whether dual protection (ear muff used over ear plugs) is necessary to bring protected noise exposures down to safe levels.
While in-ear dosimetry comes at a cost in both price and time needed for implementation, the technology allows safety managers actually to document the protected noise exposure of every employee every day. Initial results from the field indicate an immediate halt to the progression of workplace hearing loss.
TIP: For bottom-line defense against workplace hearing loss, consider in-ear dosimetry.
For these companies, success in hearing conservation was not simply defined as implementing an OSHA-compliant program. Instead, success has been defined as preventing noise-induced hearing loss, both on and off the job. Thinking out of the box, and with the commitment of management, these companies have taken hearing conservation to a new level of worker safety.
This article appeared in the October 2006 issue of Occupational Health & Safety.
This article originally appeared in the October 2006 issue of Occupational Health & Safety.