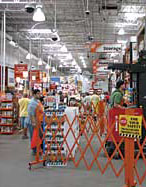
The Lowdown on Backup Alarms in Retail Stores
Alternatives such as broadband alarm frequencies seem appropriate. Try to follow new technologies.
- By Barrett Miller
- Jul 12, 2007
JUST before Christmas, I went to purchase supplies at a "big box" retailer. As I turned a corner to enter a wide aisle, I saw a narrow forklift coming toward me. It was moving too fast for a retail store. The driver was traveling with forks trailing but looking behind him. He was laughing. I heard no alarm. When the forklift was 20 feet away, the driver was still unaware of my existence. He continued to drive. I screamed. He turned his head.
When he saw me, he panicked for a moment, then swerved radically. He never slowed down. Following him, at a dead run, was a woman getting into a reflective vest. She, too, was screaming at him to stop so she could get in front and lead. She was the spotter. He turned a corner and disappeared. The woman was still running behind in a panic. I doubt that she ever caught him. By coincidence, I was on my way to investigate an accident where a lift truck had hit a shopper in a big box retailer's store. I am glad it was 10 o'clock in the morning and not noon, with its heavy Christmas crowd.
Reverse alarms on powered industrial trucks are loud, annoying, and create workplace stress. After a day on the job with several vehicles in service, alarms create fatigue and even, perhaps, physical illness. That may be the reason a dealer says backup alarms are useless. He tells us that one out of three has been altered by the users and when they are repaired, the operator quickly disables them. Visual backup alarms are no better. Together, they add a level of stress that can make a work site an awful place to be. Still, they save lives.
Forklift accidents and death are common in retail stores. In one Houston accident, an astronaut was crushed and became permanently disabled when drivers at a hardware store nudged the content from a shelf with a forklift where he was shopping.
Accidents that do not involve employees are not legally reportable except in California. Among forklift accidents that produce reportable injuries, 35 percent involve vehicle-pedestrian collisions. In Great Britain, where recordkeeping is more exacting, there are about 25,000 injury-producing accidents caused by industrial vehicle backups in an average year. NIOSH reports about two deaths per week in industrial applications because of forklift operations. OSHA statistics show there are about 680,000 forklift accidents each year and 90,000 reportable injuries.1 These don't include death and injury to customers shopping at big retail stores similar to Sam's Club, Wal-Mart, Lowe's, Home Depot, and Costco. Accidents with powered industrial trucks are almost always serious and expensive.
Incidents Hard to Track
Last year, I investigated a number of lift truck accidents and looked for common causes. In Hawaii, an 80-year- old man had stepped out of a row of pineapples in front of a forklift. The victim liked his work and did it without an accident for 50 years; he planned on forever doing the work he loved. The warehouse where he was picking up fruit for a local market was dark, space was restricted, and there were many blind spots. The spotter was off for the day. A traditional alarm was of limited value because the truck had to travel both forward and reverse continuously and there were unending blind spots. The steel warehouse was noisy. The victim had age-related hearing loss, which limits response to high-frequency signals. The victim says he could not hear the forklift, but the driver says the alarm was working. Other witnesses said the alarm was often disconnected. No one can say for sure whether the alarm functioned. Fortunately, our victim wasn't killed.
In a second incident, a highly paid cabinet maker was killed in the storage area of a retail store. He was using a skill saw. The area was congested and noisy. As the driver turned the corner, the victim was in the driver's blind spot and the spotter was otherwise occupied for just a moment. The forklift was equipped with a backup alarm that was functioning according to SAE specifications. The rear-view mirror was broken. The victim was hit by the ballast as the flat turned the corner; John Garcia died leaving four children. In a lawsuit that followed, one lawyer sued his own expert for losing the case and extracted a settlement.
In late December, a shopper looked at merchandise in the garden department of a big box hardware retailer. Because the company did not want to impose loud noises on its patrons, it had substituted a backup strobe as an alternative. It worked only in the reverse direction. (Outside, a strobe provides little information.) The backup alarm did not function in the direction of travel; his spotter had stopped to help a customer. The driver did not touch the horn as he approached a blind spot. As the victim stepped around the corner in the garden department, the driver was moving forward to set down the load. The forklift ran completely over the victim, but he survived.
Forklift accidents that happen at big box stores are frequent and are seldom reported in ways that can be easily discovered. A recent statistic from a major big box retailer may help us understand the degree of danger and extent of risk in these stores: During one three-year period, as reported under court order, 100 persons were injured by forklifts in its Florida stores. The chain had only 65 stores in the state. The victims of these accidents were often shoppers. Fourteen of these incidents eventually became civil suits, and 80 of the incidents became worker's compensation claims. Remember, this was only one chain in only one state.
Moving Beyond OSHA's Requirements
Readers will recognize a number of OSHA violations; most involve simple human failure. They also will recognize that alarms are only a partial solution.
These are some of the common factors: First, our examples happen in tight spaces. Each had a spotter diverted for a moment for what seemed to be an important reason. Each happened when the forklift was driving with a load in the direction of the forks. All vehicles were equipped with backup alarms when they left the factory. All had legally required safety equipment. Each had a working horn. What was needed was redundancy.
Historically, OSHA has not required the installation of a forklift alarm.2 A driver must keep a view of the direction of travel and stop at blind spots and cross aisles, and sound his horn. If a powered industrial truck was purchased with an alarm and other safety devices, original safety features must be maintained. It is permissible to replace a safety device with another that provides equivalent or greater protection so that the alarm can be heard "above ambient sound levels." It was no surprise, then, that if an original backup alarm could not be heard, neither could a louder device.
There are new alternatives. It is important to use a spotter, for example, though there is no legal requirement. It is important to move merchandise only when customers are not in the store, but this practice is suspended most of the time. We need to be aware of new technology. A recently approved alarm device is available that offers a partial solution to these seemingly diverse causes. In the next few paragraphs, we will look at a new type of forklift alarm that can minimize human error in the application of proximity alarm systems. These alarms actually reduce the overall sound level.
An English company has met the spirit and letter of codes and standards for U.S. markets, and its product is now being sold in the United States. It is accepted by OSHA, MSHA, and SAE. This didn't happen overnight; typically, an alarm had to meet SAE requirements for volume and frequency and the words "heard above," as used in OSHA memoranda, seemed impossible in light of manufacturers' alarms that operated at an ear splitting 85-115 decibels. Here, we are talking about an alarm that might be used in a large retail store where the ambient sound level never goes above 65 dBA. The new method is far quieter; it could be 68 dBA, for example, and thus more within the normal range of sound and a great deal less imposing.
In its enforcement practice, OSHA tells us the alarm should be heard over ambient sounds and must be the functional equivalent of original equipment. The company's alarm has a better idea that both operates at a lower level and projects a signal in a different pattern. The sound itself is complex; the manufacturer calls it white noise or broadband sounds. The complex tones, projected at lower frequency, make the alarm from 10 to 50 dBA less intrusive. The frequency of the sound pattern is less likely to vibrate off of environmental objects and is more directional. These audible alarms can be made to function in both forward and reverse directions.
Human Factors
A few years ago, I looked at an alarm on an expensive yacht in the Bahamas. An alarm had sounded, and the boat had sunk in 1,000 feet of water. In the 200-square-foot salon, two 115 dBA alarm sirens with different frequencies projected sounds at the captain at once. No one could interpret the emergency audible alarm. The captain and crew heard an alarm condition that was so intense, it was debilitating.
As they tried to find the source of the danger, they became confused and helpless. They could not use 50 years of experience to interpret the alarm signal. The Coast Guard responded and saved the crew, but the boat was lost. Accidents like this one should convince us: Systems designed around human capacity and behavior sometimes outrank standards accepted by committee.
Backup alarms on industrial equipment are addressed in standard J994 of the Society of Automotive Engineers (SAE International).3 Until recently, the new theory of alarms was not accepted. But strong, consistent information on human behavior must change opinions. OSHA recognizes the new alarm method; so does MISHA. New, quieter alarms eventually won a community service award for innovative environmentally friendly technology.
In the case of the British company's alarm, acceptance was based upon an examination of human factors (capacity) and private laboratory certifications. The company introduced evidence of ISO standards (ISO 7731:2003(e)). The words broadband simply mean that a mixture of frequencies are blended as an alarm signal rather than using a single piercing frequency.
For brevity, I will list several of their positive arguments. Each has been stated in human behavioral terms:
• Sound pollution is now considered a major health hazard.
• Broadband alarms avoid the shrill sounds associated with traditional alarms.
• Broadband alarms are more directional.
• When there are several lift trucks, listeners can distinguish the source difference.
• Broadband alarms are more easily heard by older people.
• Broadband alarms are already accepted as an alarm system (and there are other brands).
• Broadband signals don't ricochet in the manner single tones do.
• Broadband signals are less likely to produce panic reactions.
• Broadband signals produce less stress.
• Broadband sounds are less objectionable in outside areas.
Conclusion
In most cases, it is possible to put off material delivery until there are no customers in the store, but big box stores have special needs. They often move material while the store is occupied by customers. Aisles must be blocked off when a forklift is used. In these cases, proximity alarm can be used in both directions. Because the peak sound level in big box stores is only 65dBA, traditional alarm volume is too loud; sound levels can be reduced. Lower the volume of audible alarms and manipulate the frequency range. Each 3dBA reduction in sound results in a reduction of sound intensity of 50 percent.
Alternatives such as broadband alarm frequencies seem appropriate. Try to follow new technologies. Finally, your company must be careful not to create new problems, so make changes in small increments.
Although not legally required, a spotter is vital in big box operations. If merchandise must be moved while the store is open to the public, add a spotter. The relationship between the forklift driver and the spotter is unique. It's like a dance--a slow dance. The spotter becomes the driver's eyes and makes contact with the driver by maintaining eye contact with the driver most of the time. One hopes the spotter also stops pedestrians from walking into the path of the forklift and keeps himself or herself from becoming a victim.
Finally, once the forklift has arrived in an aisle where it will be used, isolate the forklift by closing the aisle to pedestrians. When your work is completed, move the forklift back to its assigned parking spot to prevent trip-and-fall accidents.
References
1. Forklift Awareness, OSHA 1997.
2. Letter to William Overby, 8/13/04, from Richard Fairfax, Directorate of Enforcement programs, OSHA.
3. Recommended Practice: Alarm-Backup-Electric-performance Test, and Application-SAE J994-85.
This article originally appeared in the July 2007 issue of Occupational Health & Safety.